Ключевые узлы
Асфальтобетонный завод – это сложный технический комплекс, специализирующийся на производстве асфальтобетонных смесей, неотъемлемых компонентов дорожного строительства. В его основе лежит сложный процесс, который начинается с подготовки и смешивания различных ингредиентов, таких как минеральные заполнители, вяжущие материалы и добавки. Эти компоненты тщательно отбираются и сочетаются в соответствии с требованиями качества и характеристиками конечного продукта.
«Мерко Руссланд» уделяет особое внимание ключевым компонентам установок. Сушильный барабан, горелка, грохот, фильтр, система управления идеально соответствуют друг другу и гарантируют безупречную работу и высокую производительность оборудования для выпуска асфальта.
Важным аспектом работы асфальтобетонного завода является его экологическая безопасность. Многие заводы используют современные технологии, чтобы минимизировать выбросы вредных веществ в атмосферу и водные ресурсы.
АБЗ – это ключевое звено в инфраструктурном строительстве, обеспечивающее высококачественные материалы для строительства и ремонта дорожных покрытий, а также прилегающих объектов.
Агрегат питания
Агрегат питания является одной из ключевых составляющих асфальтосмесительной установки, играя важную роль в начальной стадии производства асфальтобетонных смесей. Его основная задача — обеспечить бесперебойную и точную подачу инертных материалов (таких как щебень, песок) на завод для дальнейшей обработки.
Агрегат питания включает несколько важных компонентов, каждый из которых выполняет свою специфическую функцию.
- Бункеры для хранения материалов. Обычно агрегат питания оснащается несколькими бункерами, каждый из которых предназначен для хранения определенной фракции инертных материалов. Это позволяет поддерживать постоянное наличие необходимых компонентов для производства.
- Дозирующие устройства. Эти устройства регулируют количество материалов, подаваемых из бункеров на конвейерную линию. Дозаторы обеспечивают точное измерение каждого компонента, что важно для соблюдения рецептуры асфальтобетонной смеси.
- Конвейерная система. Конвейеры транспортируют инертные материалы от бункеров к следующему этапу производства. Конвейерные ленты могут быть различной длины и конструкции, в зависимости от компоновки завода.
- Контрольные системы. Современные агрегаты питания оборудованы системами автоматического контроля, которые обеспечивают точную настройку и мониторинг работы всех устройств. Это позволяет оптимизировать процесс подачи материалов и минимизировать ошибки.
Функции агрегата питания
Агрегат питания выполняет несколько ключевых функций в процессе производства асфальтобетонных смесей.
- Бесперебойная подача материалов. Один из основных аспектов работы агрегата питания — обеспечение постоянного потока инертных материалов на завод. Это необходимо для поддержания непрерывного производственного процесса и предотвращения простоев.
- Точное дозирование. Дозирующие устройства позволяют точно измерять количество каждого компонента, что критично для получения качественной асфальтобетонной смеси. Точность дозирования влияет на физические и эксплуатационные характеристики готового продукта.
- Автоматизация процесса. Благодаря современным системам управления, процесс подачи материалов можно автоматизировать. Это снижает влияние человеческого фактора, уменьшает вероятность ошибок и повышает общую производительность завода.
Агрегат питания играет ключевую роль в обеспечении эффективности и качества производства асфальтобетонных смесей. Его работа напрямую влияет на несколько важных аспектов.
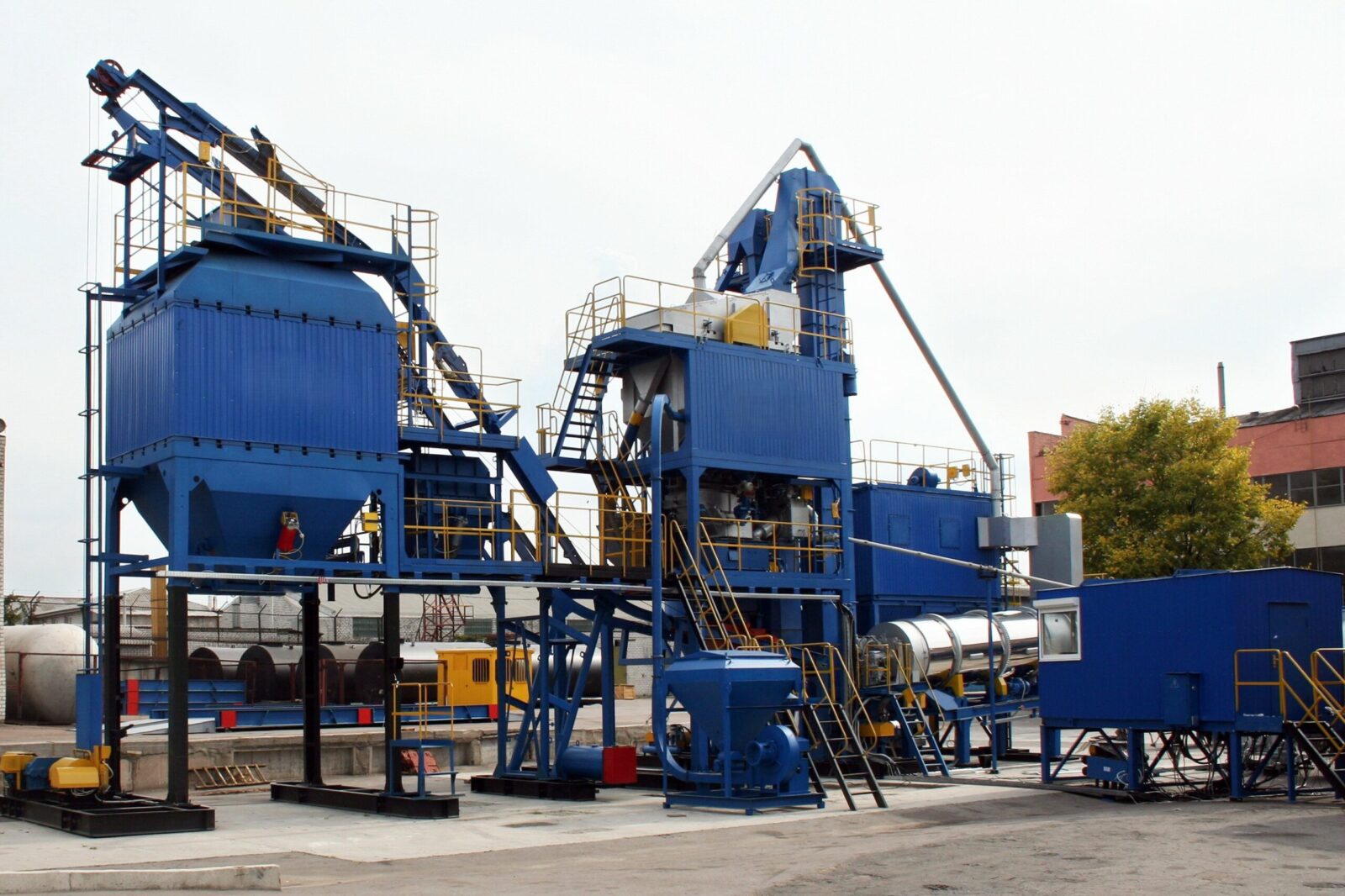
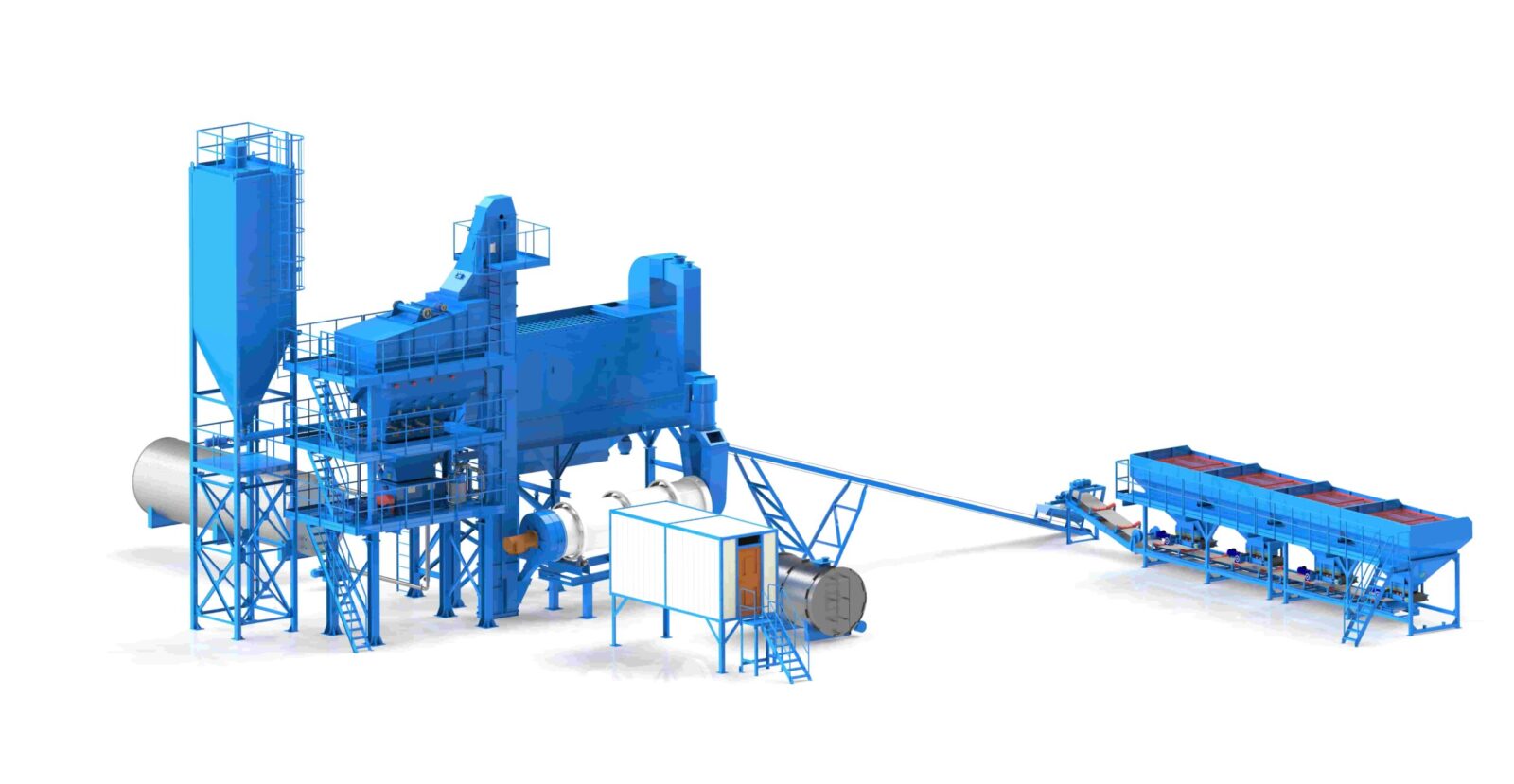
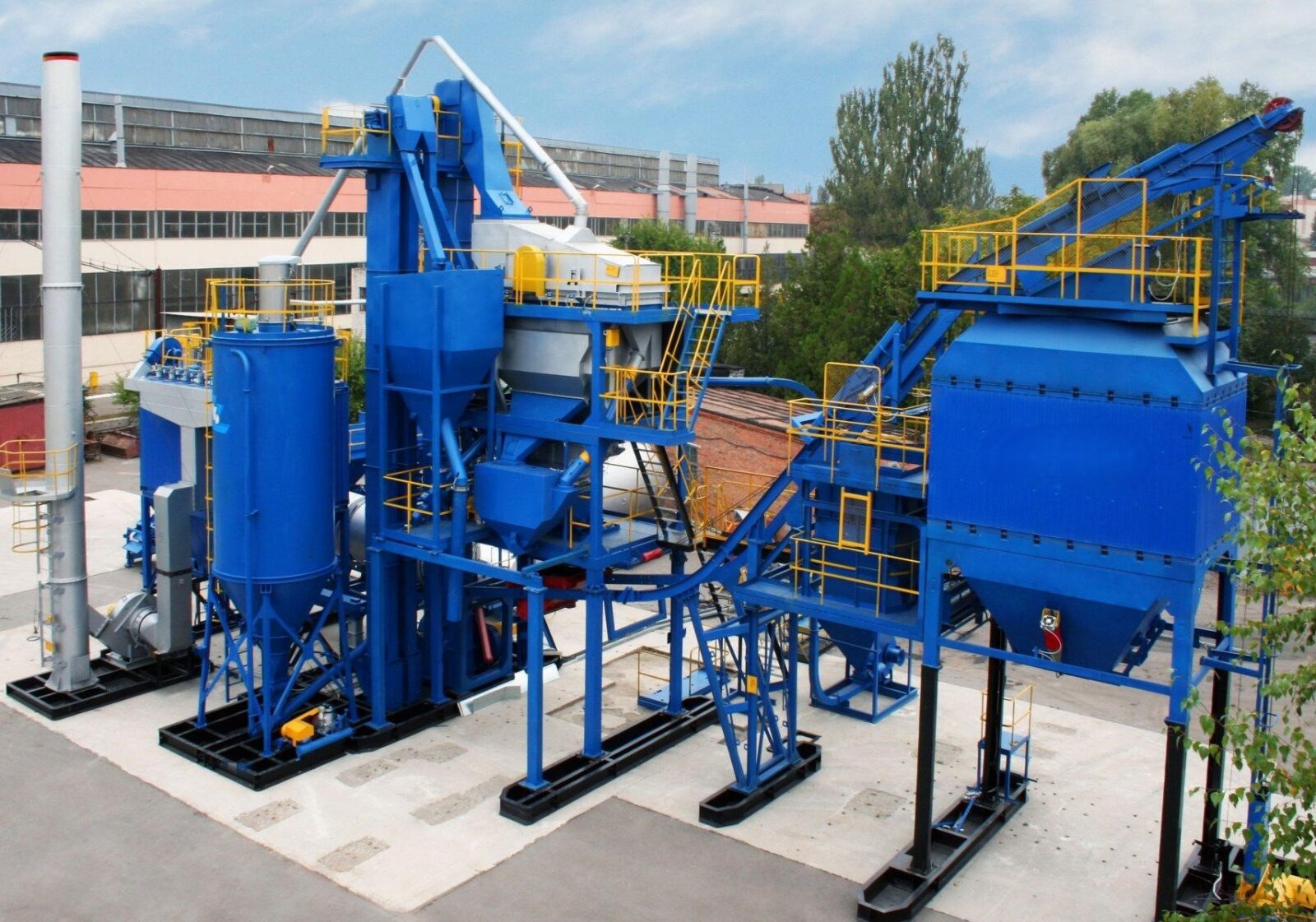
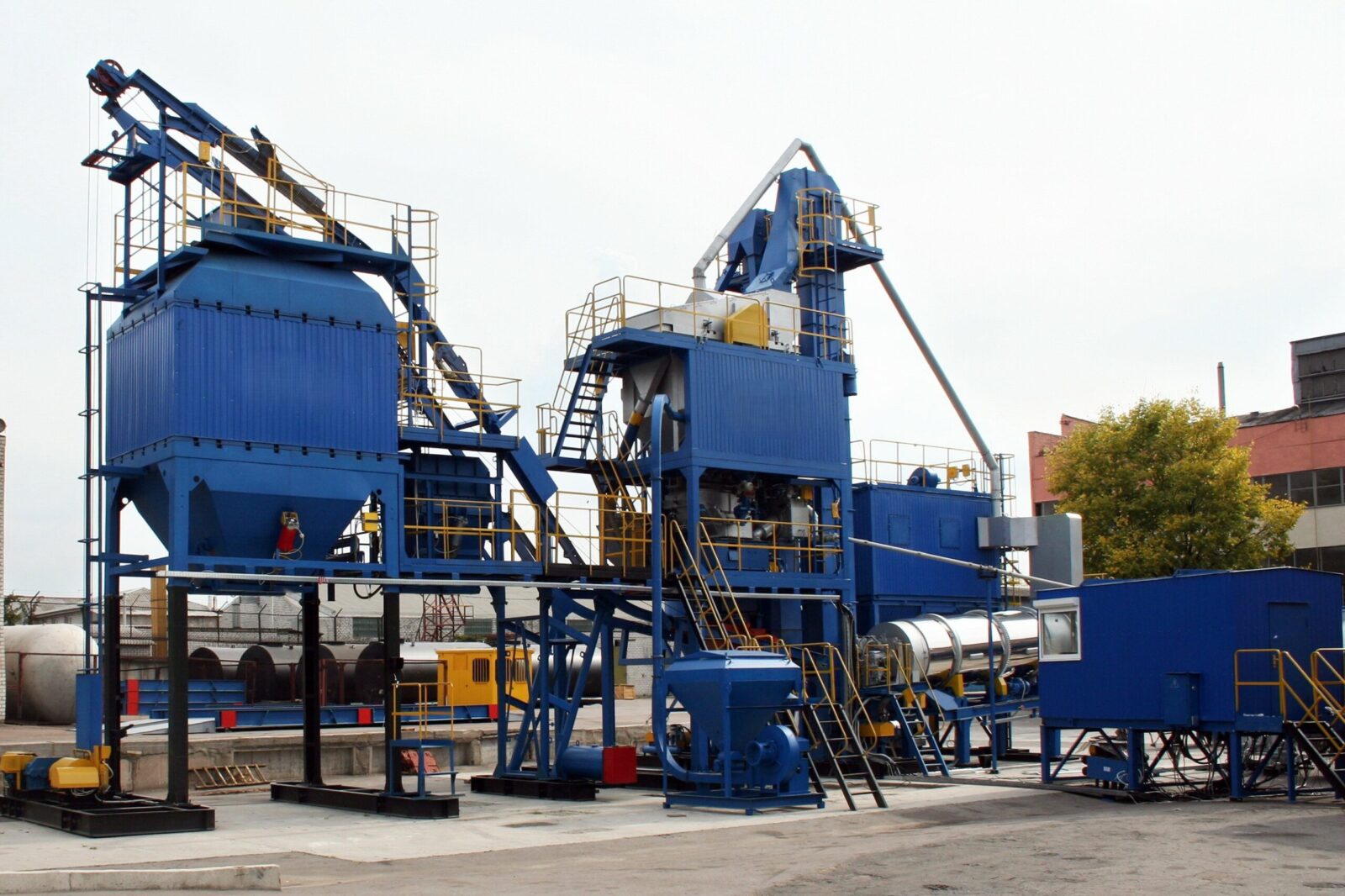
Сушильный барабан и горелка
Сушильный барабан и горелка – это ключевые узлы в работе асфальтобетонного завода, играющий важную роль в подготовке минеральных материалов для производства асфальтобетонной смеси. Эти компоненты предназначены для сушки инертных материалов, таких как песок, щебень, перед их использованием в смеси.
Устройство сушильного барабана
Сушильный барабан представляет собой цилиндрическую конструкцию с внутренним обогреваемым пространством. Внутри барабана располагаются специальные лопатки и грабли для перемешивания инертных материалов по его длине. Это позволяет равномерно распределять материалы и обеспечивать их равномерное просушивание.
Принцип работы
Процесс работы сушильного барабана и горелки основан на принципе теплообмена. Внутри барабана материалы подвергаются воздействию теплового потока, который идет от горелки. При этом влага, содержащаяся в материалах, испаряется, что приводит к их сушке. Лопасти внутри барабана перемешивают материалы, тем самым обеспечивая испарение влаги. Пары воды и пыль, которые выводятся из барабана через системы вентиляции и фильтрации, предотвращают загрязнение окружающей среды.
Значение сушильного барабана и горелки в производстве
Сушильный барабан и горелка играют ключевую роль в производстве асфальтобетона по нескольким причинам.
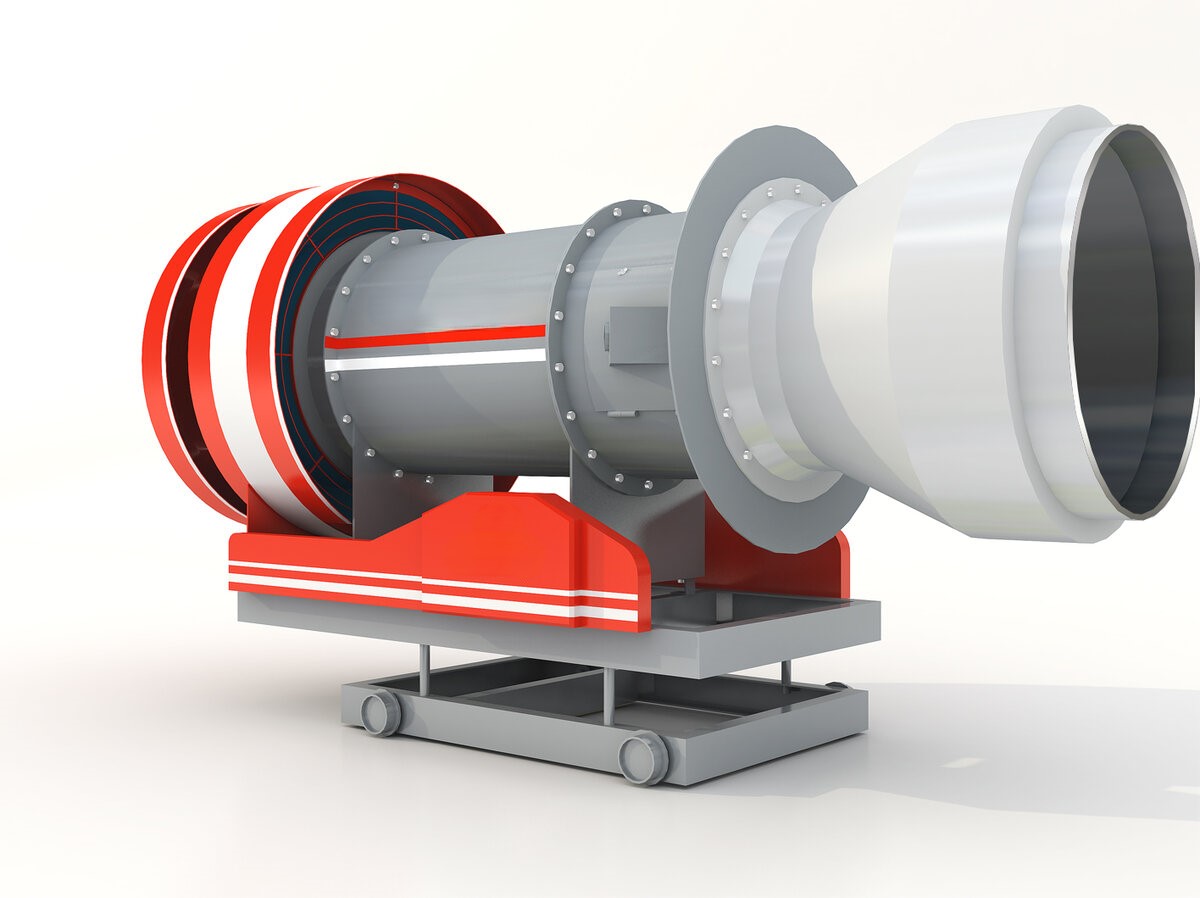
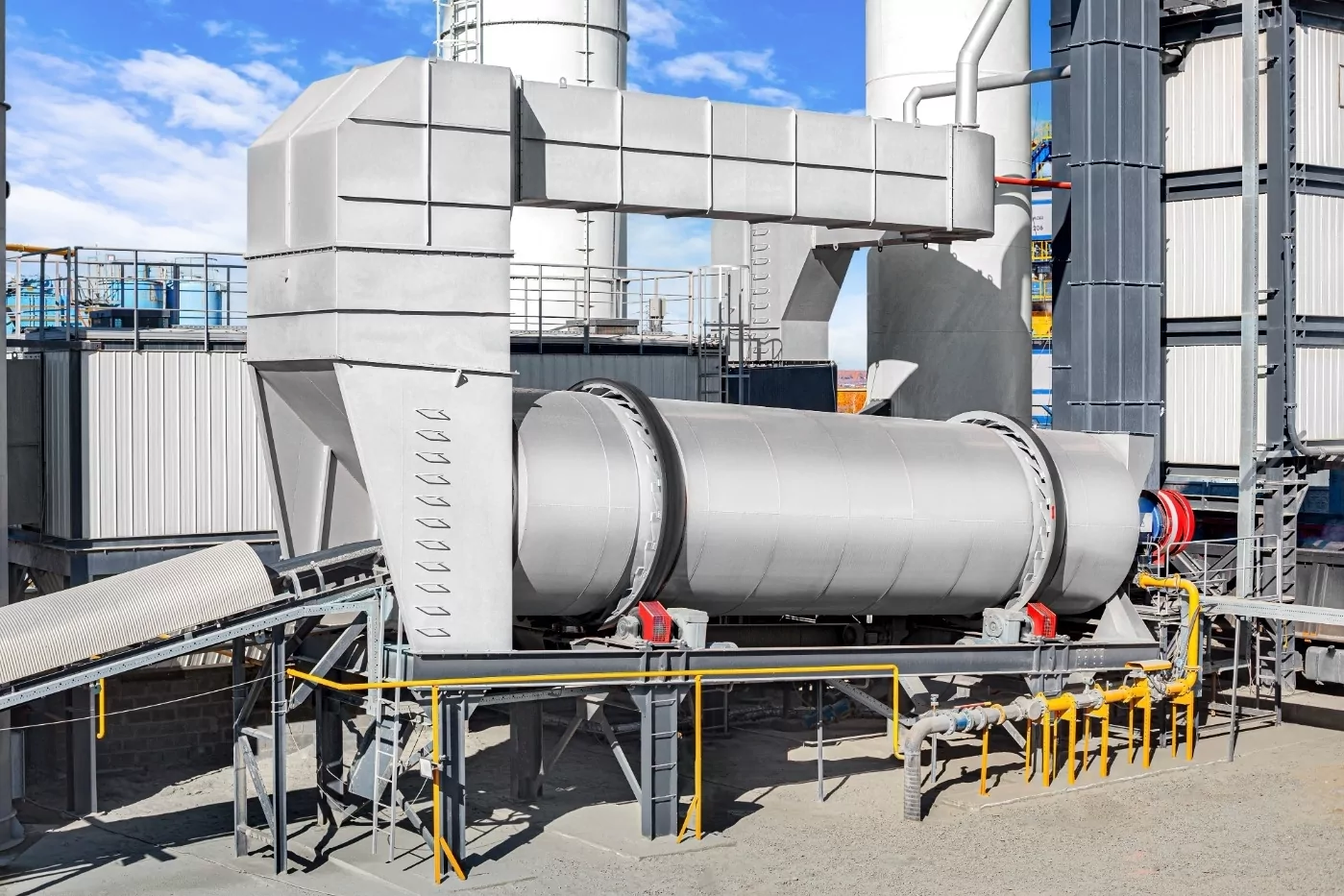
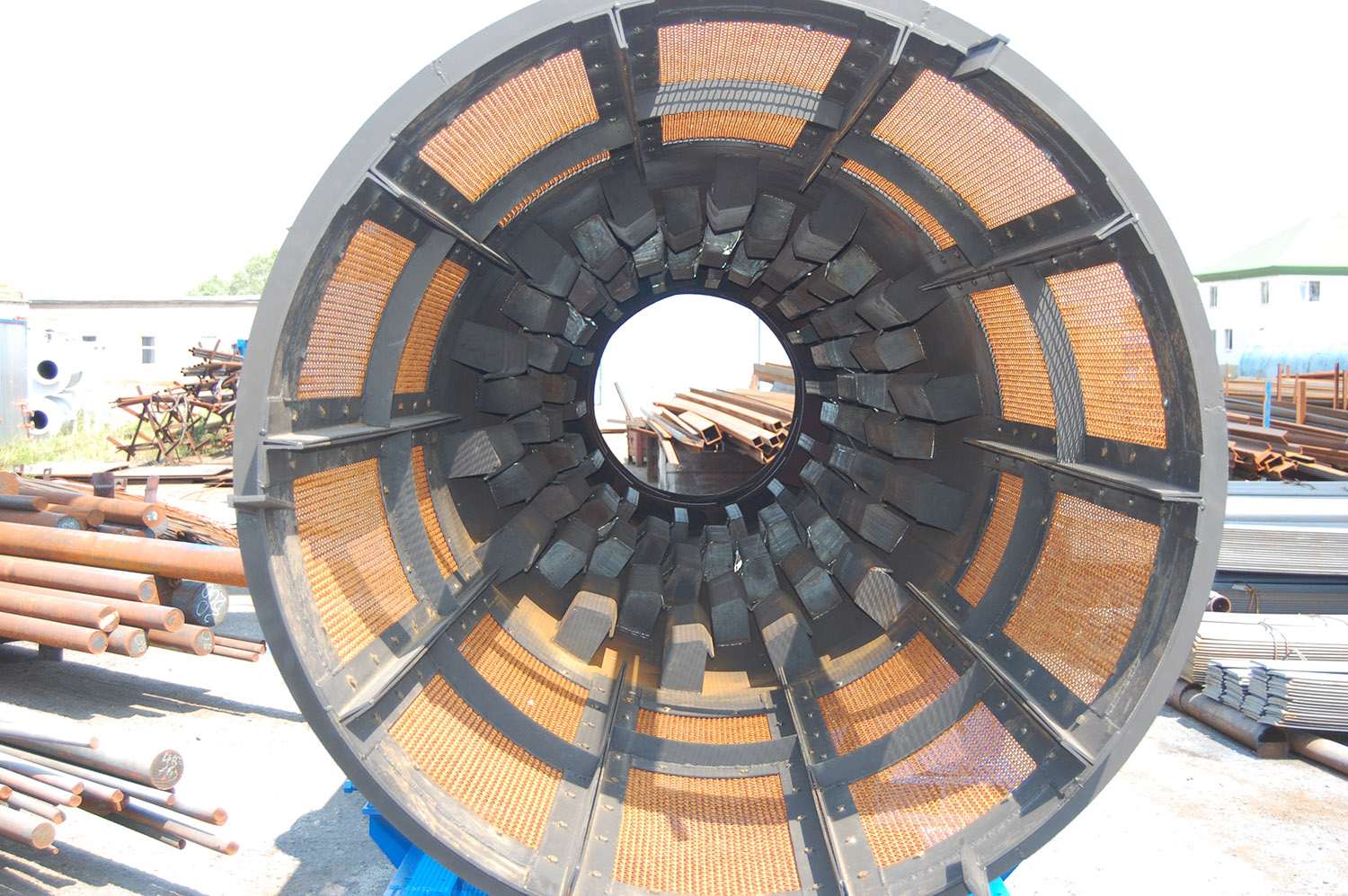
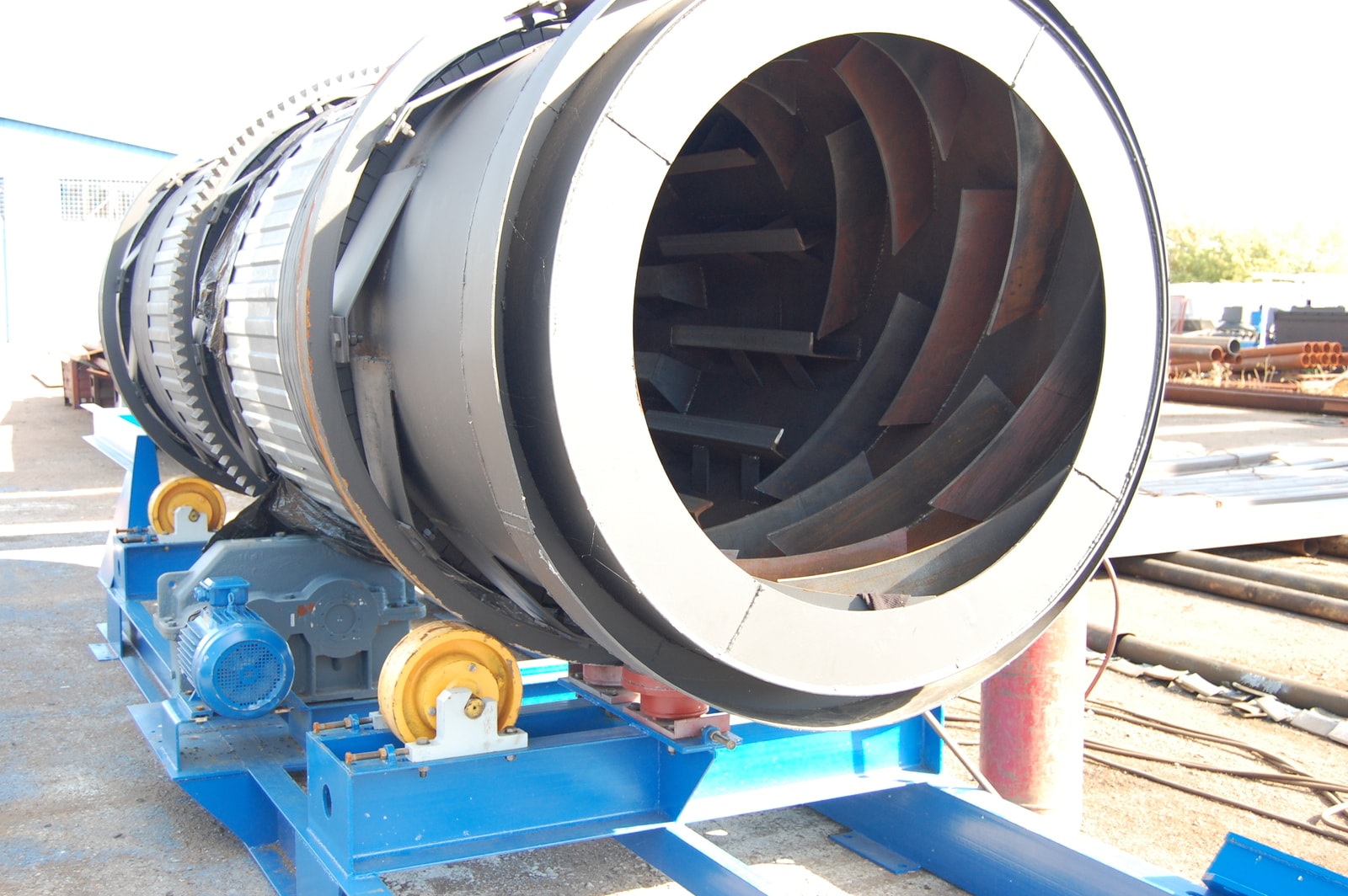
Система пылеочистки
Система пылеочистки является важной составляющей АСУ, обеспечивая эффективное удаление пыли и других вредных веществ из отходящих газов, выделяемых в процессе производства. Она играет ключевую роль в соблюдении экологических норм и стандартов безопасности окружающей среды.
Основные компоненты системы пылеочистки
1. Фильтры. Это основной элемент системы, который захватывает твердые частицы пыли из отходящих газов. Фильтры могут быть различных типов, на асфальтосмесительных установках SANY в приоритете рукавные фильтры.
2. Вентиляторы. Вентиляторы создают поток воздуха, который приводит к циркуляции отходящих газов через фильтры. Они играют важную роль в обеспечении эффективного функционирования системы пылеочистки.
3. Отводящая труба. Этот компонент отводит очищенные от газов частицы пыли из системы, направляя их в безопасное место для последующей обработки или утилизации.
Принцип работы системы пылеочистки
1. Захват частиц пыли. Отходящие газы, содержащие пыль и другие вредные вещества, проходят через фильтры системы. Твердые частицы пыли задерживаются на поверхности фильтров, а чистый воздух проходит через них.
2. Накопление пыли. Пылевые частицы, задержанные на фильтрах, накапливаются со временем, что может привести к уменьшению эффективности системы. Для предотвращения этого необходимо периодически проводить очистку фильтров посредством пневмоудара. Замена фильтров нужна только в случае их разрыва.
3. Удаление пыли. Очищенный воздух выводится из системы через вентиляторы, а накопленная пыль отводится из фильтров и направляется на утилизацию или дальнейшую обработку.
Значение системы пылеочистки и ряд важных преимуществ.
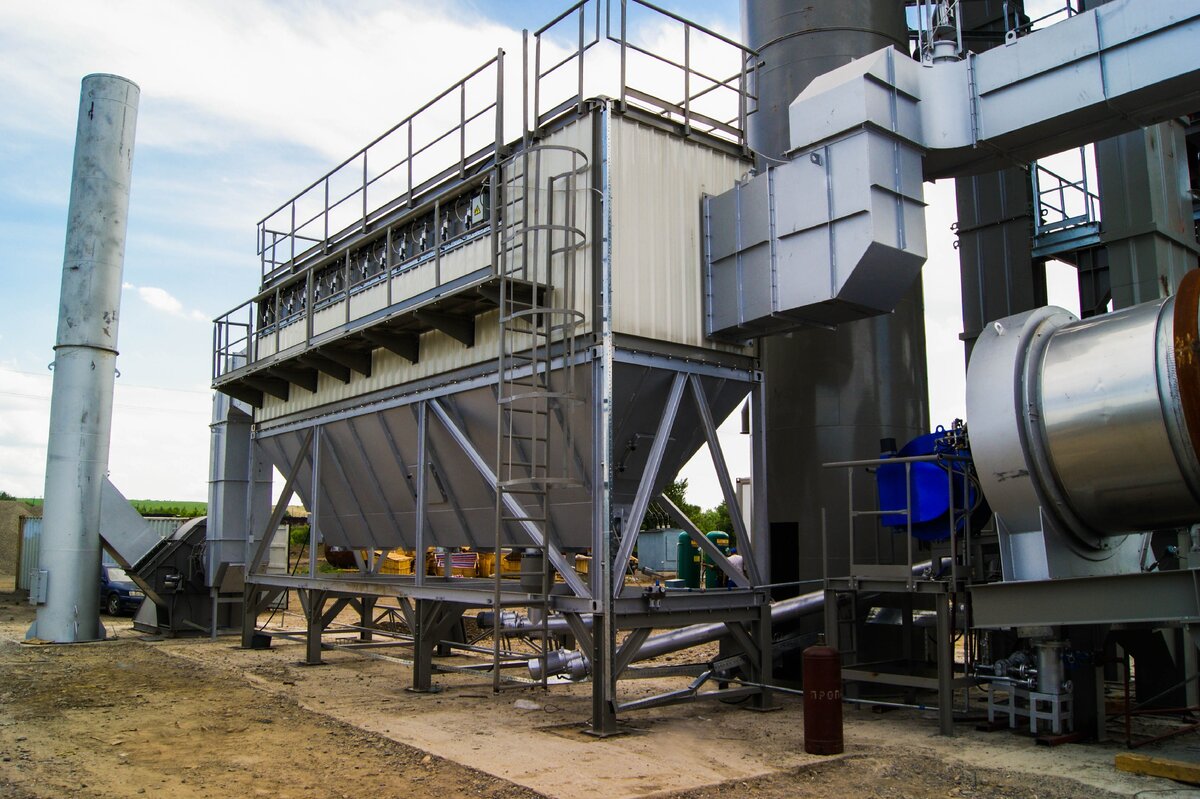
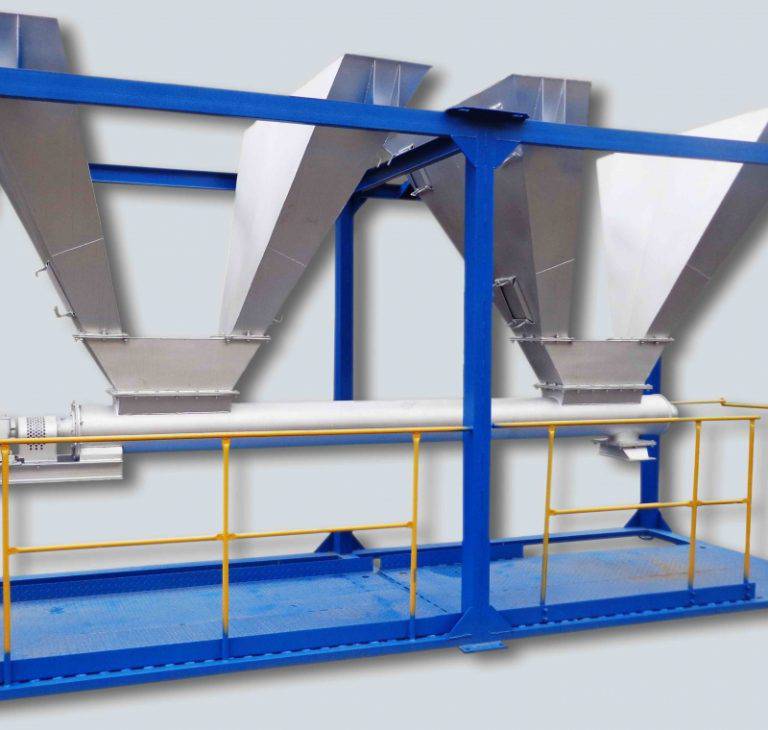
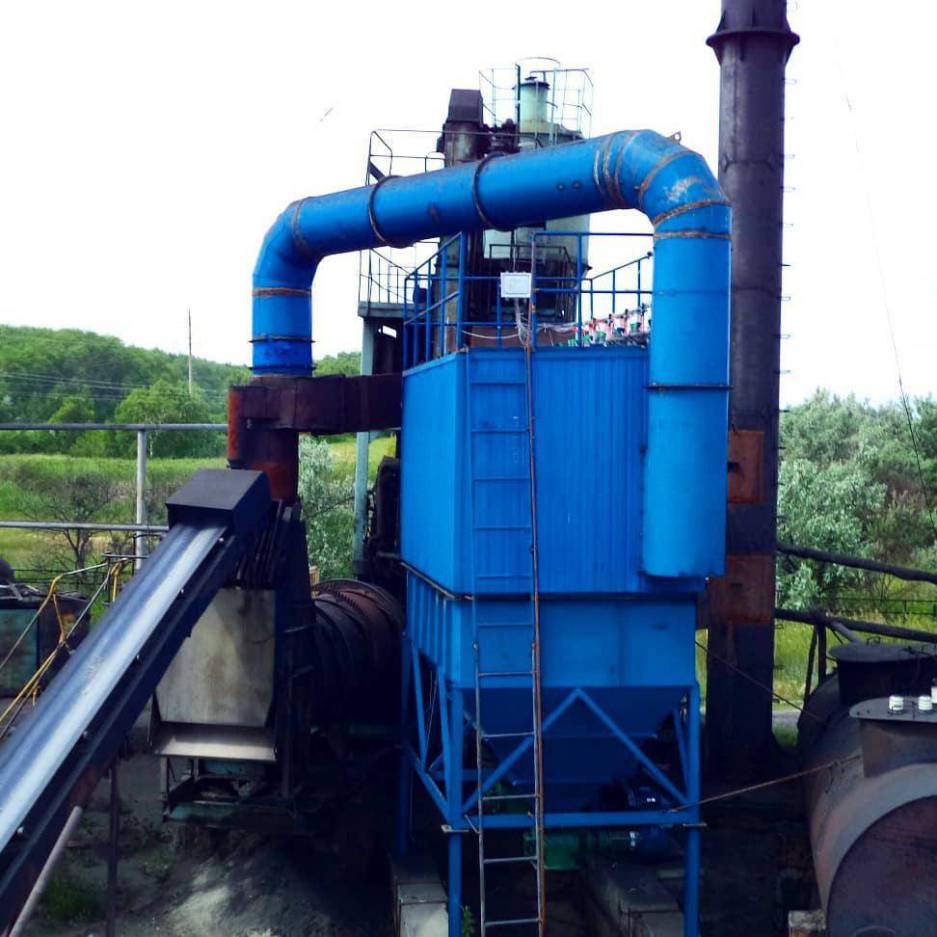
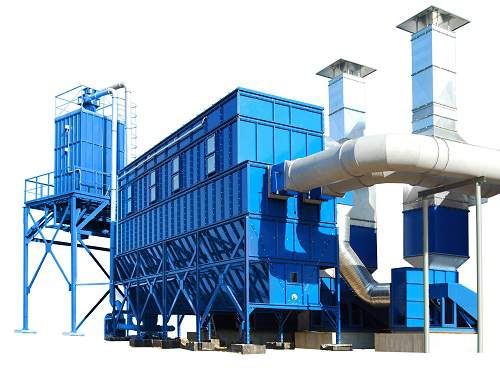
Элеватор горячих инертных
Элеватор горячих инертных материалов является важным ключевым узлом асфальтосмесительной установки, обеспечивающим подачу просушенного материала из барабана в грохот для дальнейшего распределения по фракциям.
Принцип работы элеватора горячих инертных материалов.
- Загрузка материалов: Горячие инертные материалы поступают в нижний приемный бункер элеватора прямо из сушильного барабана. Бункер обычно оснащен вибрационными или механическими системами для равномерного распределения материалов по ковшам.
- Подъем материалов: Транспортировочные ковши, закрепленные на цепях, поднимают материалы вверх. Движение ковшей обеспечивается системой привода, которая может быть электрической или гидравлической.
- Транспортировка и подъем: Ковши движутся по замкнутому циклу, проходя через нижний и верхний барабаны. По мере подъема горячие материалы сохраняют свою температуру благодаря изоляции корпуса элеватора.
- Высыпание материалов: Достигнув верхней точки элеватора, ковши переворачиваются или опрокидываются, высыпая горячие материалы в в грохот для дальнейшей сортировки по фракциям и подачи к смесителям.
- Возвращение ковшей: Пустые ковши возвращаются в нижнюю часть элеватора для нового цикла загрузки, обеспечивая непрерывный процесс транспортировки.
Значение элеватора горячих инертных материалов.
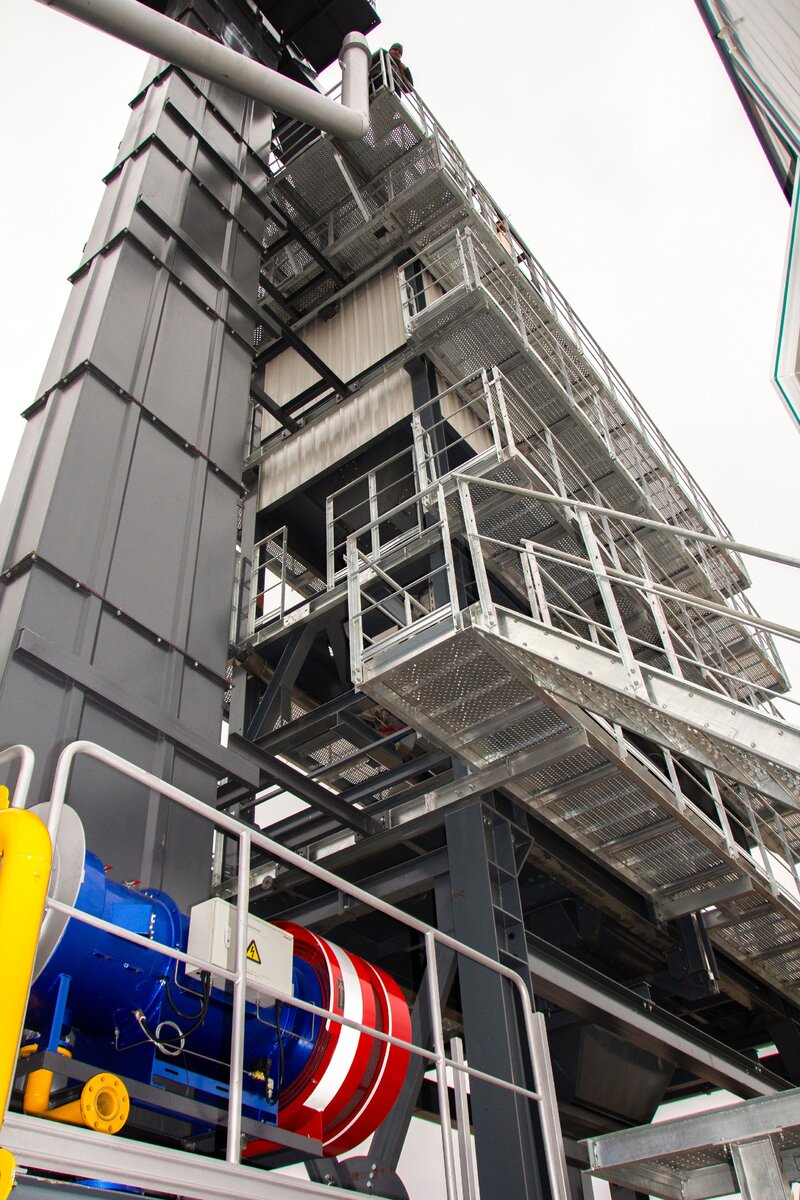
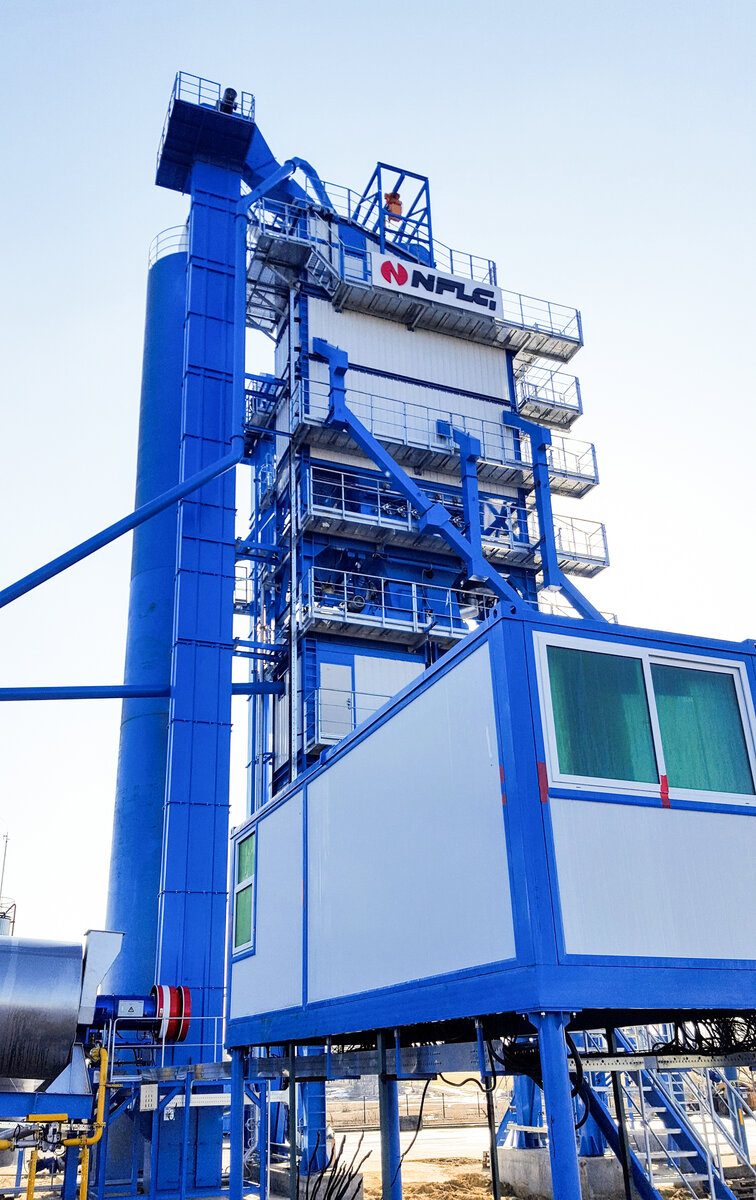
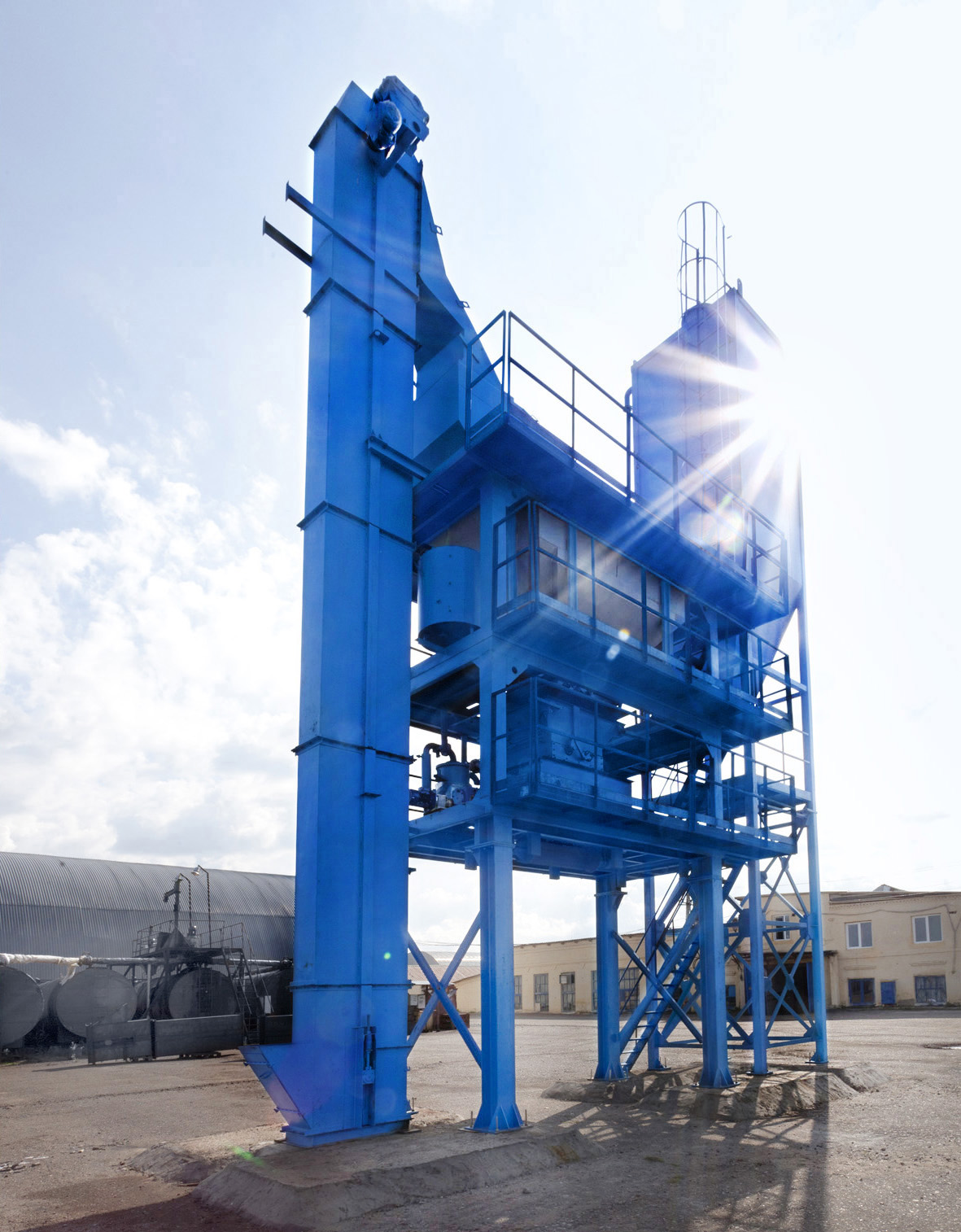
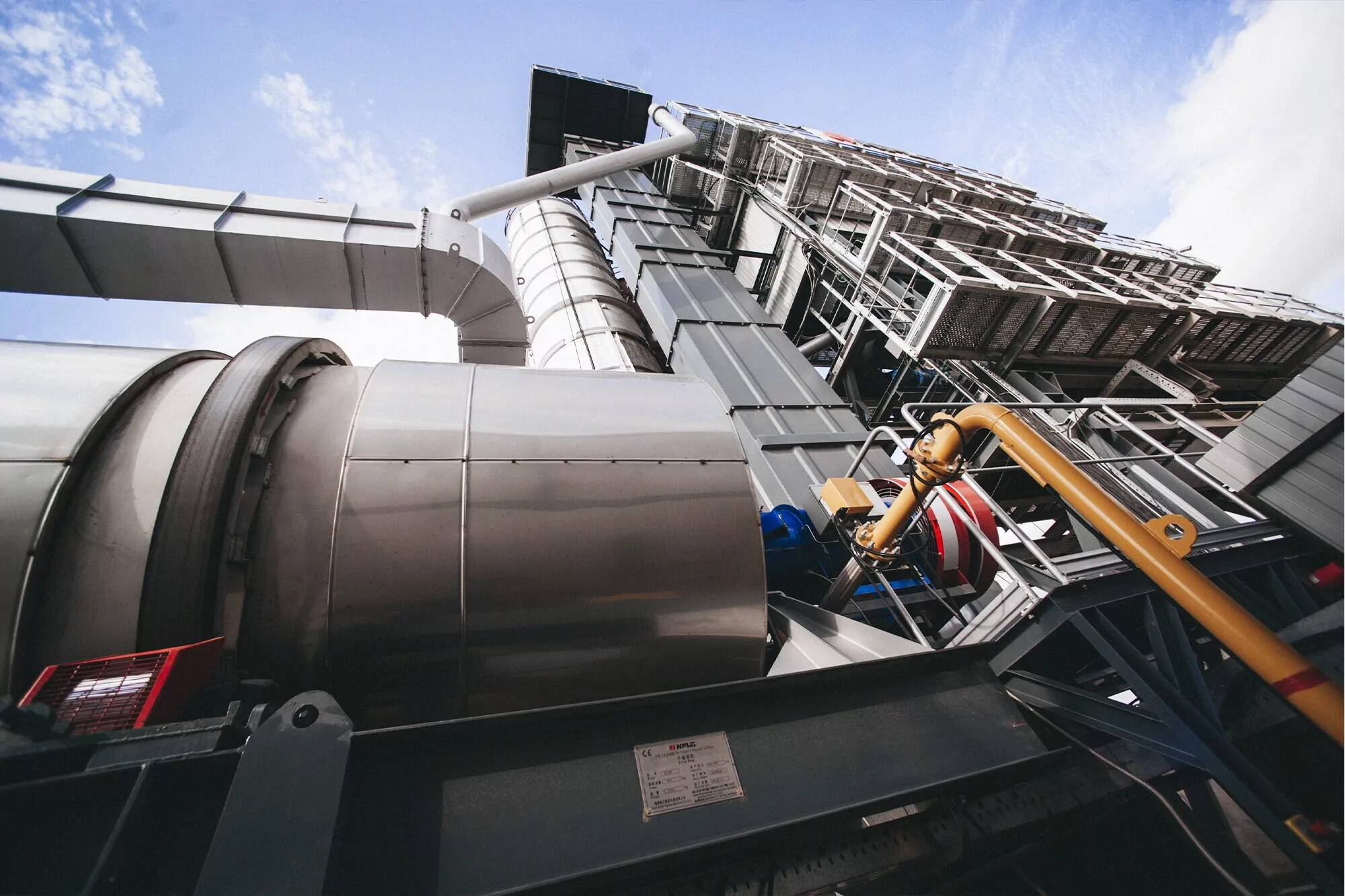
Виброгрохот
Виброгрохот – это крупный ключевой узел в работе асфальтобетонного завода, отвечающий за классификацию и сортировку инертных материалов перед их смешиванием с асфальтом. Он используется для разделения сыпучих материалов на различные фракции по размеру, что позволяет получить необходимую гранулометрическую композицию для производства высококачественного асфальтобетона.
Принцип работы виброгрохота.
Сырьевой материал поступает на виброгрохот из элеватора или другого источника. Под воздействием вибрации, виброгрохот эффективно сортирует материал на основе его размера. Большие частицы остаются на верхнем слое сита, тогда как более мелкие проходят через сито и собираются на нижнем слое. Готовые фракции материала собираются в соответствующих контейнерах или направляются дальше по производственному процессу.
Значение виброгрохота на асфальтобетонном заводе.
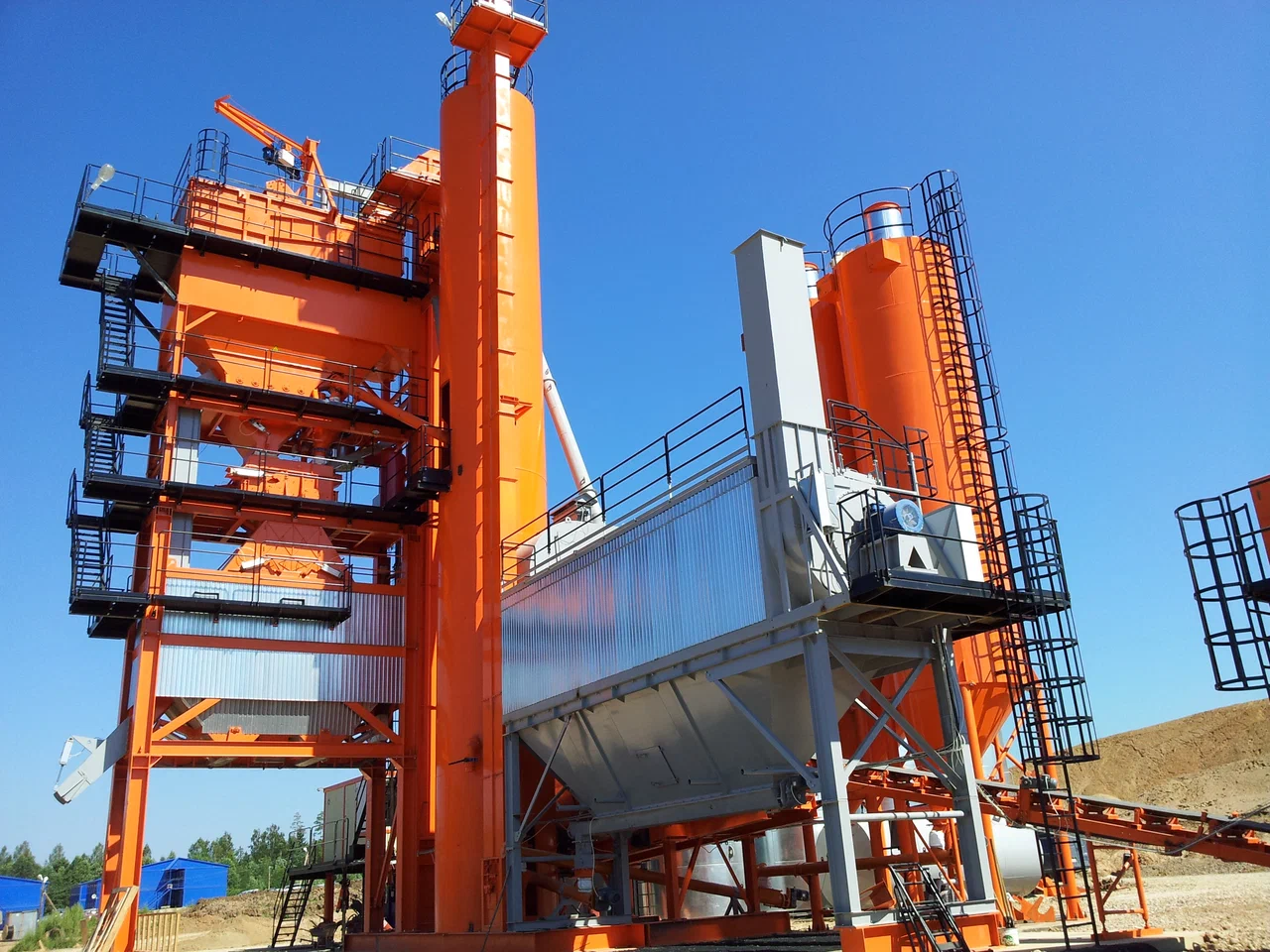
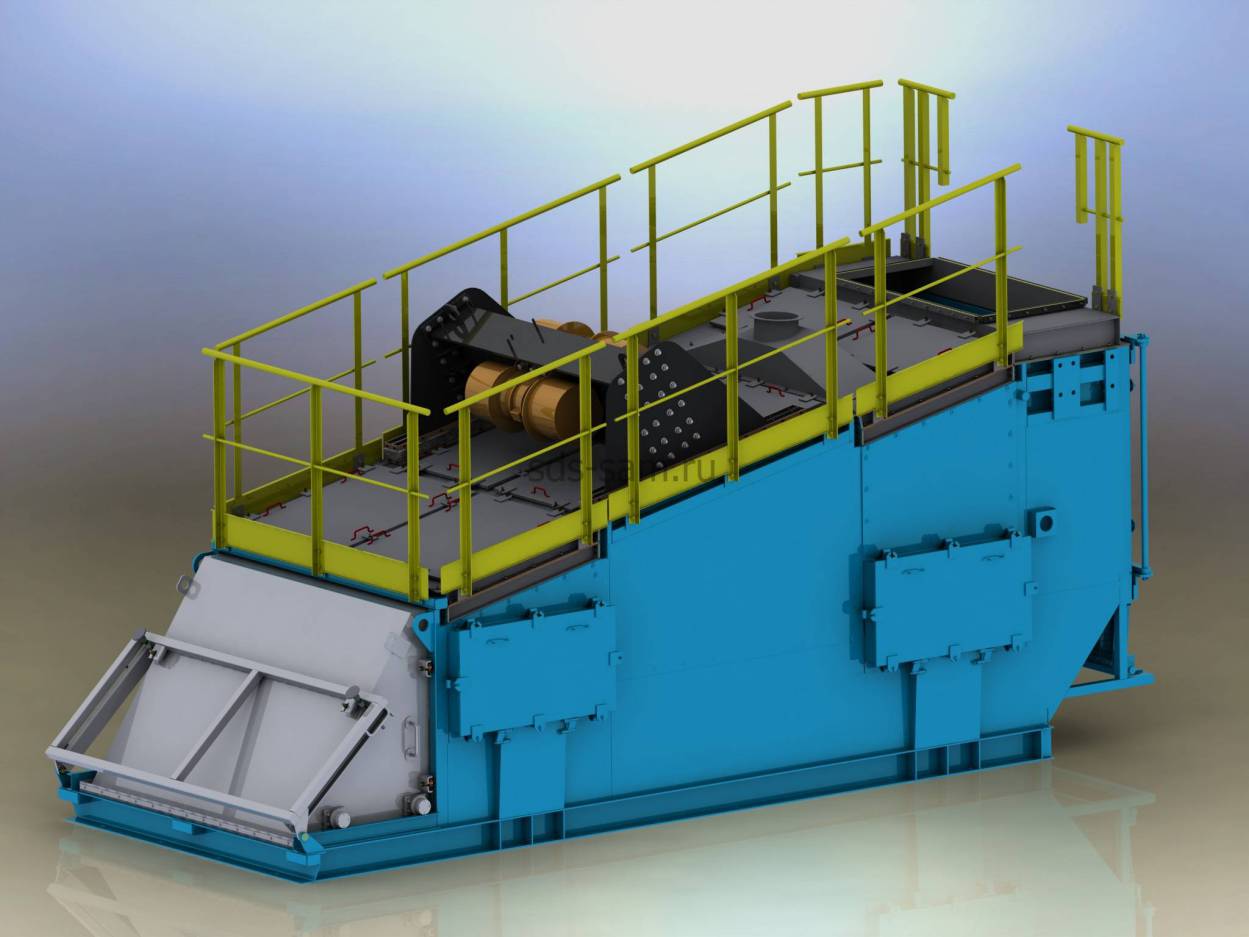

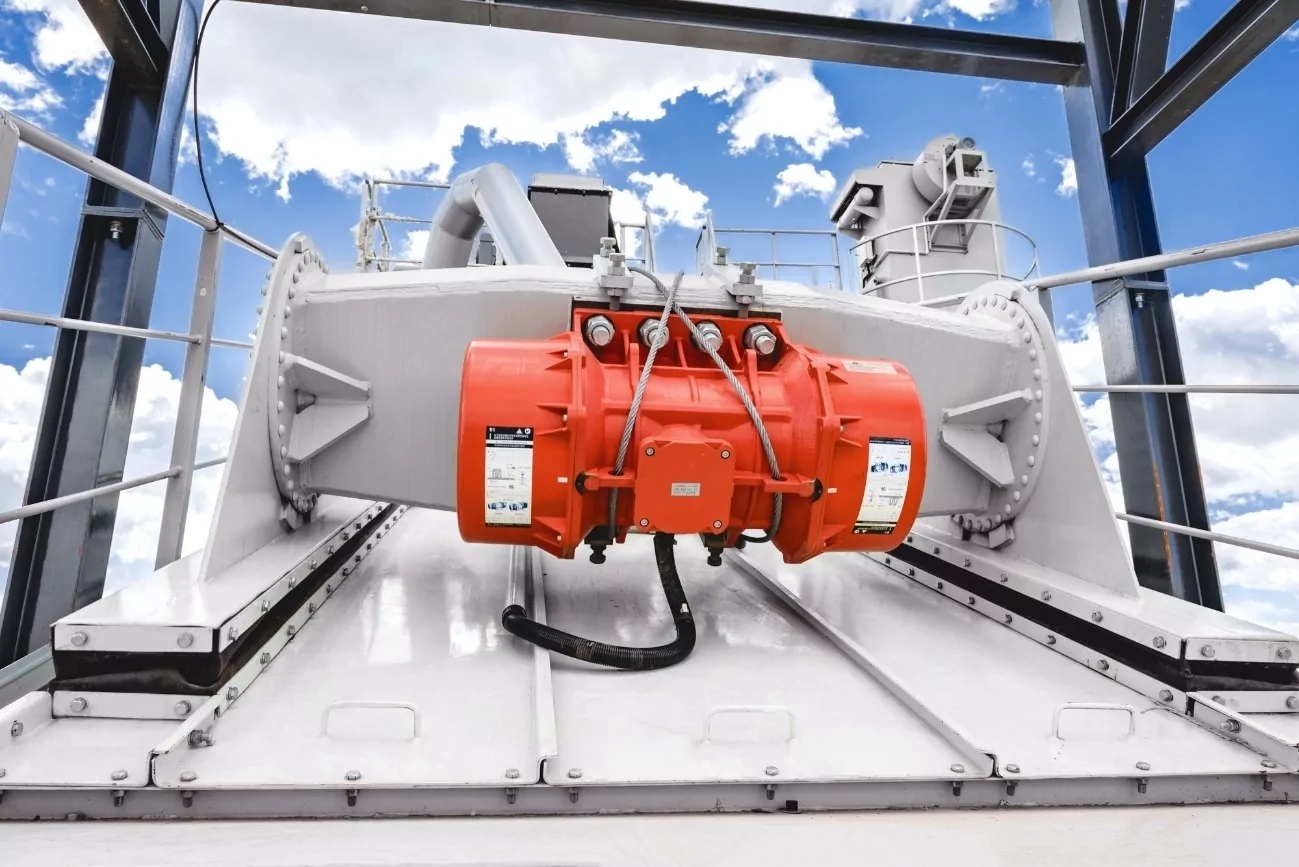
Бункер горячих материалов
Бункер горячих материалов – это ключевой элемент асфальтобетонной установки, играющий важную роль в производственном процессе. Этот устройство представляет собой специальный резервуар или контейнер, предназначенный для временного хранения и подачи горячих компонентов асфальтобетонной смеси – минеральных заполнителей перед их смешиванием с битумом.
Основная функция бункера горячих материалов состоит в том, чтобы обеспечить непрерывный поток сырья в процессе производства асфальтобетонной смеси. Горячие материалы поступают в бункер из специализированных хранилищ или сыпучих материалов, где они временно хранятся перед дальнейшей обработкой.
Критическим аспектом работы бункера горячих материалов является его способность поддерживать оптимальную температуру сырья. Поскольку асфальтобетонная смесь требует высоких температур для обеспечения качественного смешивания и укладки, бункер должен быть оборудован системами подогрева и терморегулирования, чтобы предотвратить остывание материалов и сохранить их подходящую консистенцию.
Еще одним важным аспектом является точная дозировка горячих материалов перед их подачей на следующий этап производства. Для этого бункер обычно оснащен специализированными системами контроля и автоматизации, которые обеспечивают точное соотношение компонентов в процессе подачи.
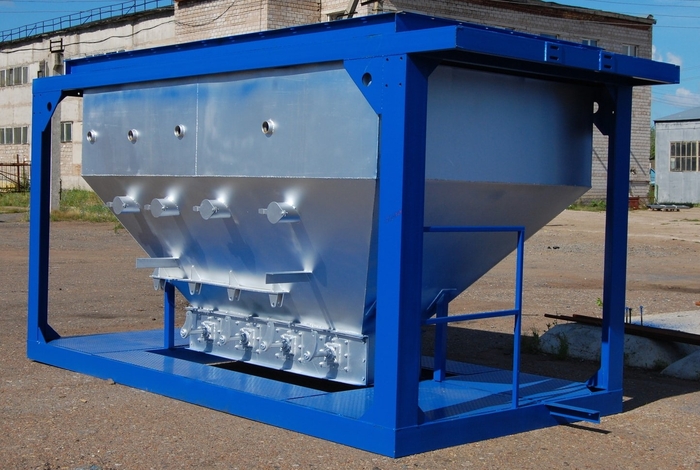
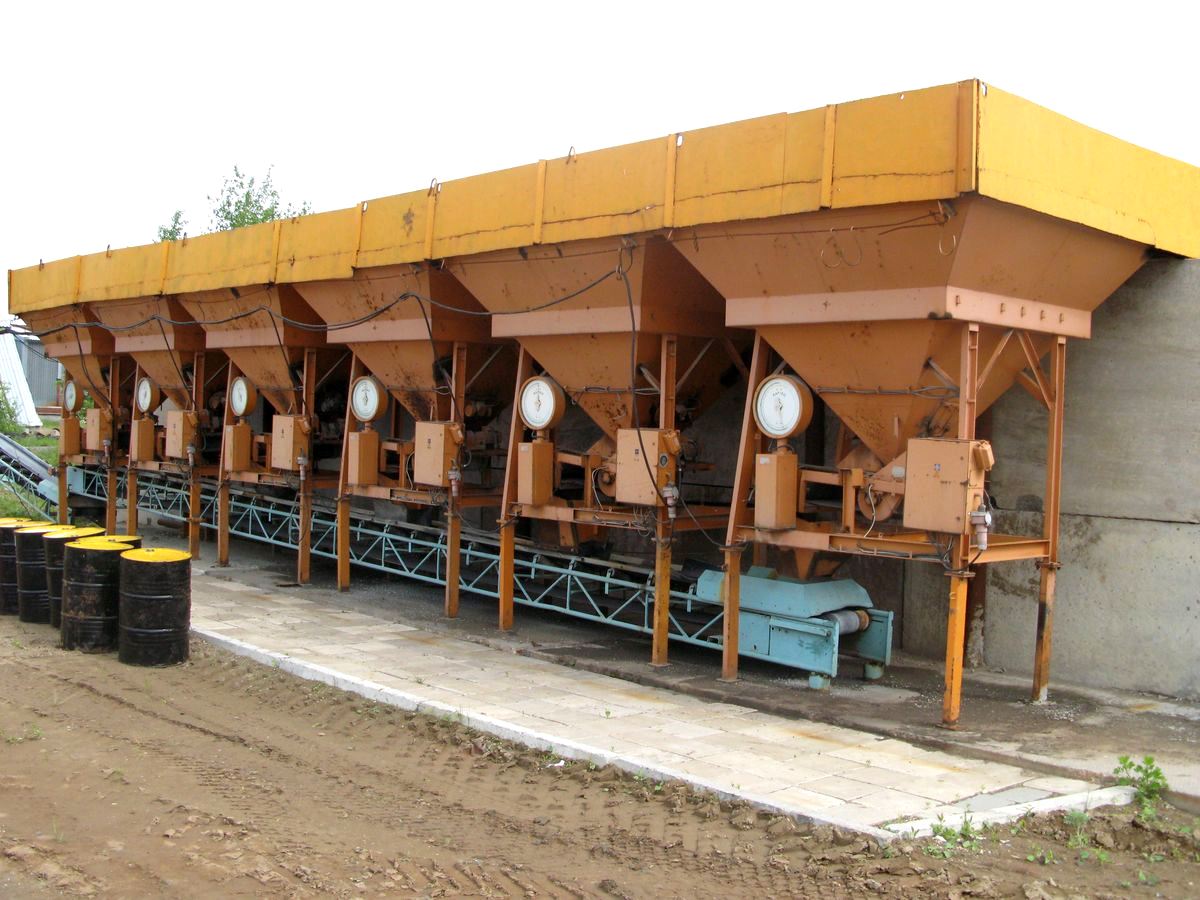
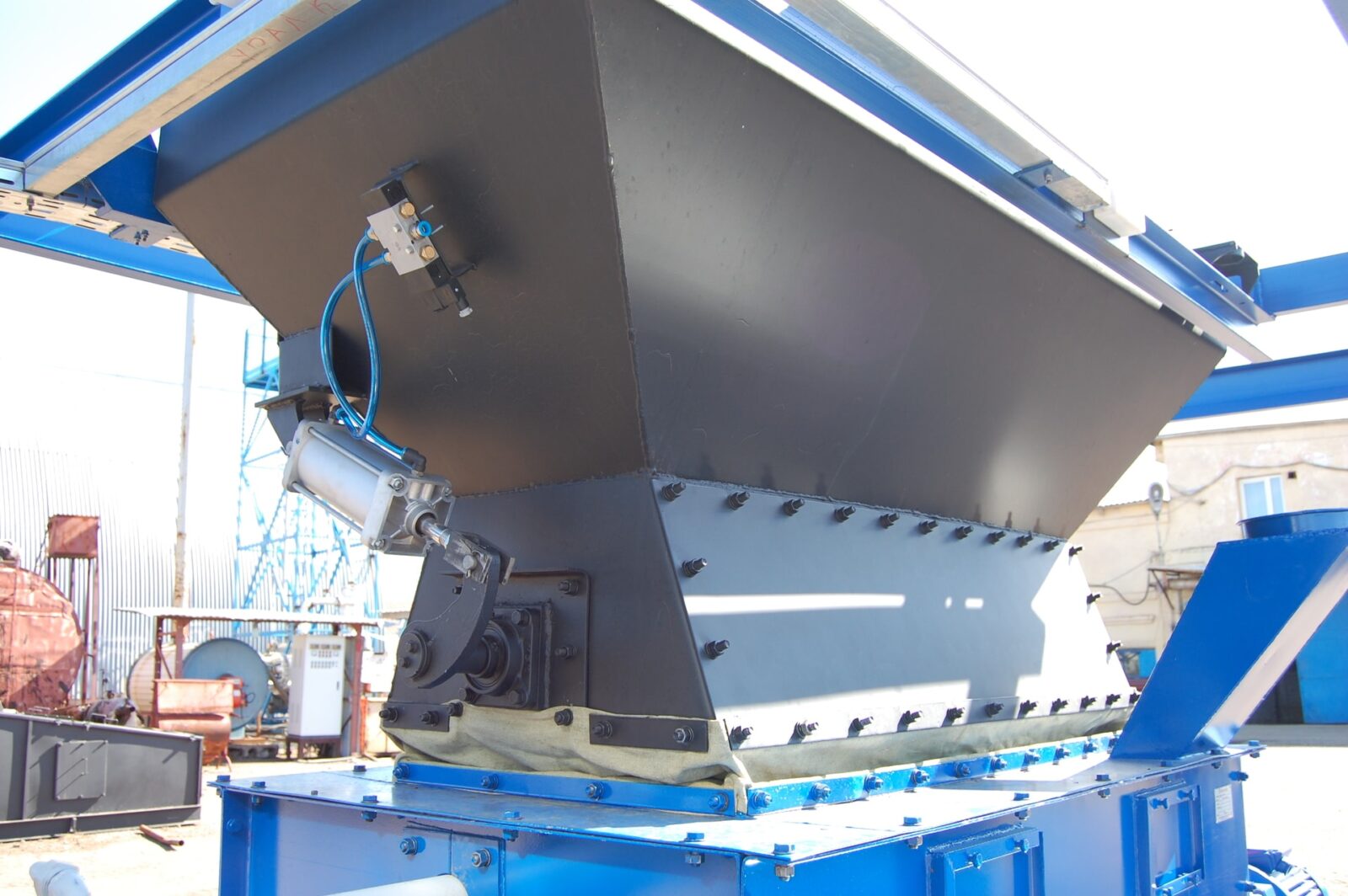
Система выгрузки на дозатор
Система выгрузки на дозатор на различных видах асфальтобетонного завода незаменима в точном и эффективном дозировании горячих инертных материалов и асфальта перед их смешиванием. Этот важный узел обеспечивает точность и стабильность процесса производства асфальтобетона, что является необходимым условием для получения высококачественного продукта. Вот некоторые основные аспекты системы выгрузки на дозатор.
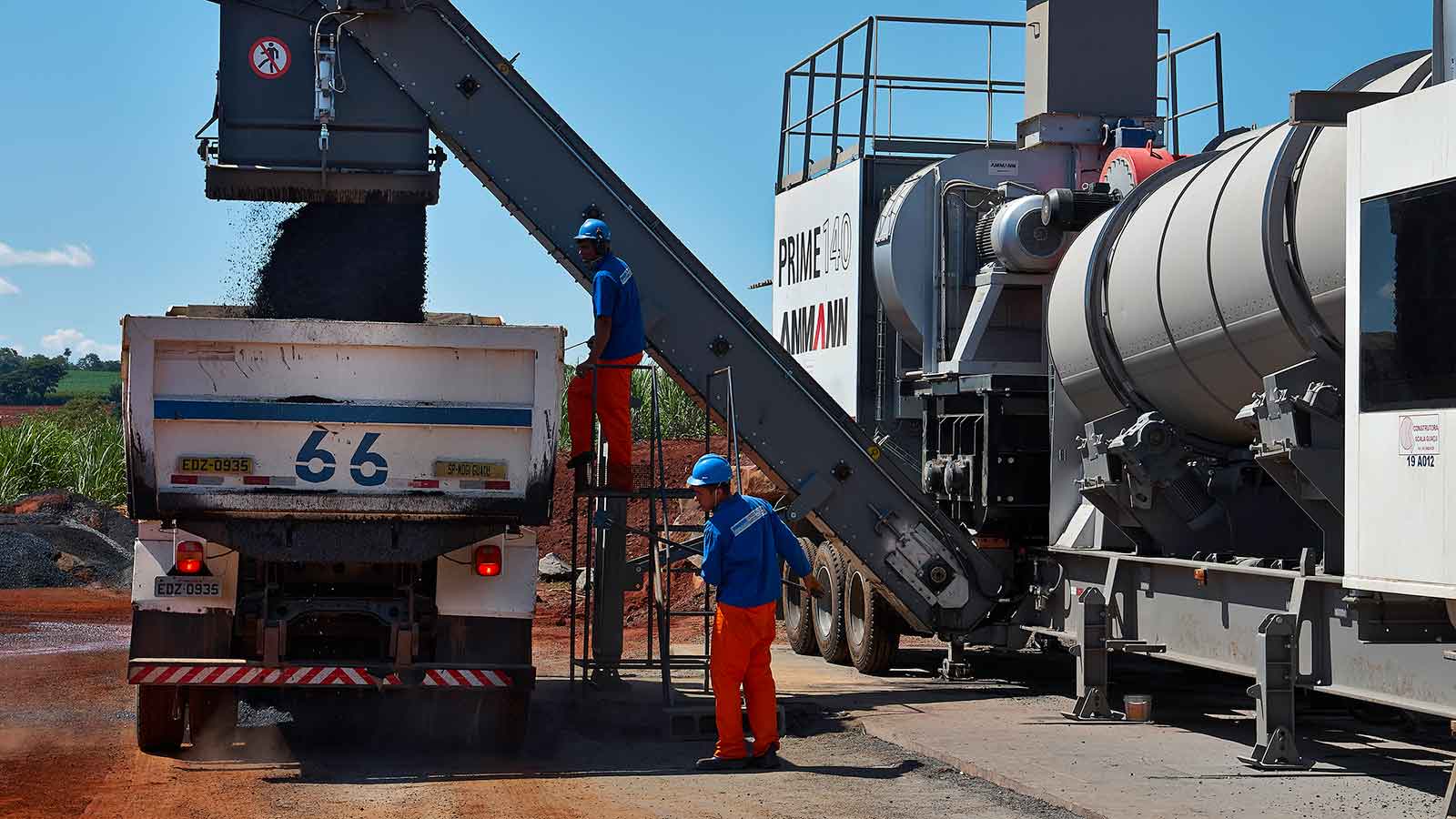
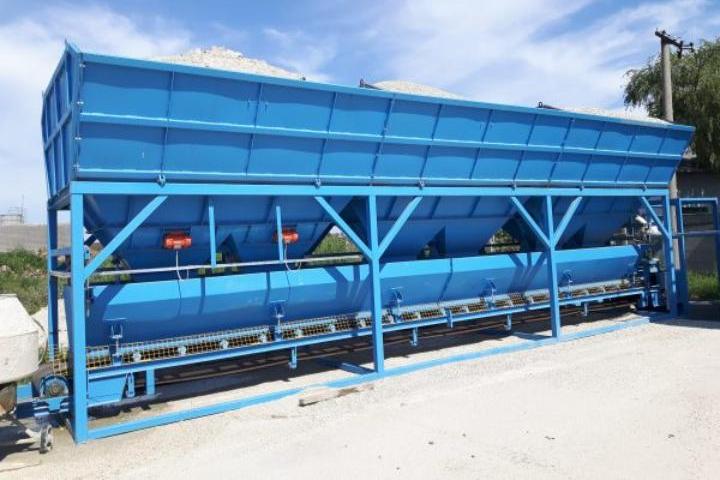
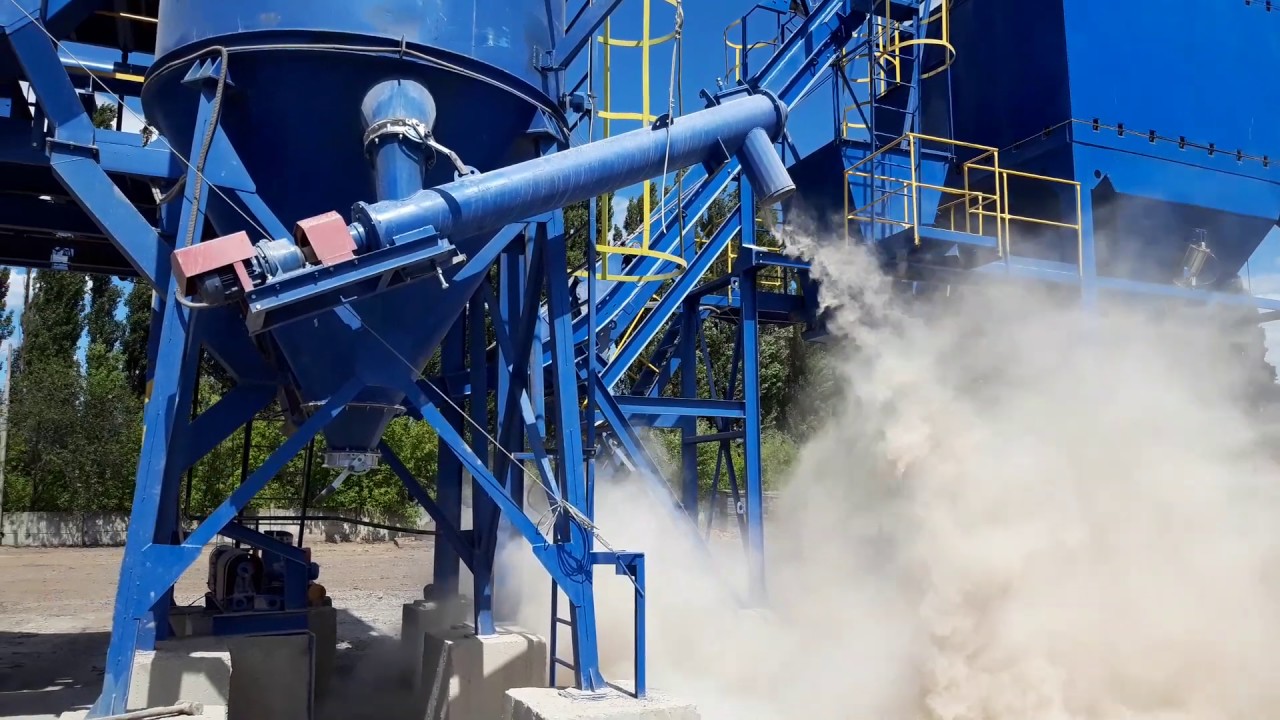
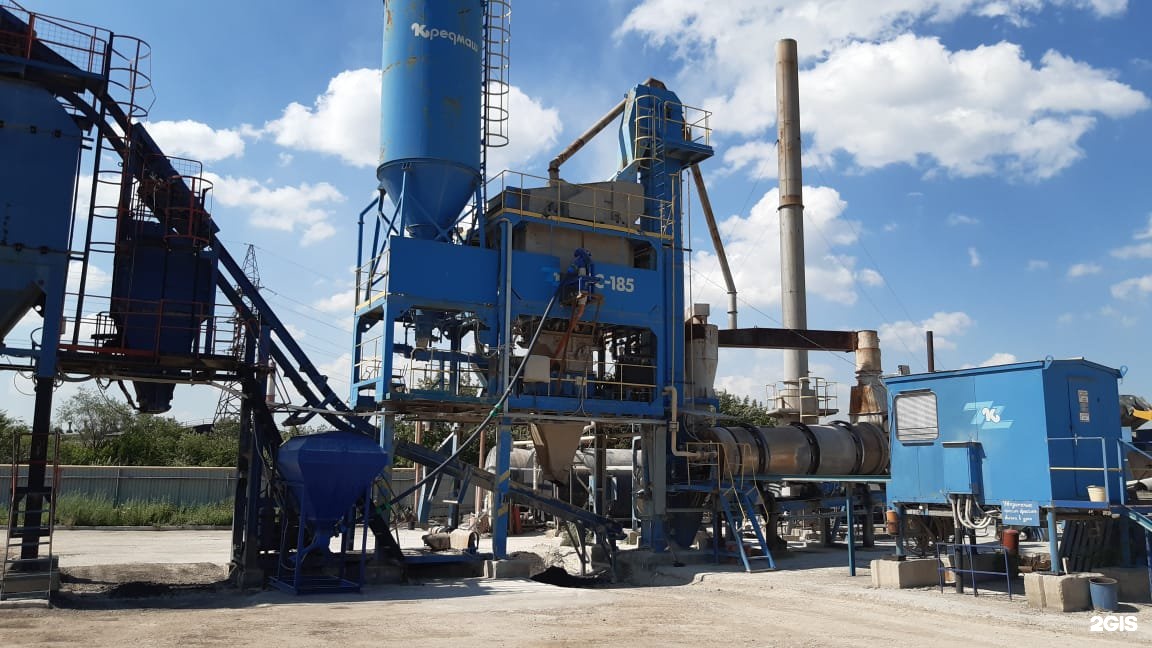
Блок дозаторов — Весы
Весы это один из ключевых компонентов в производительности асфальтосмесительной установки, отвечающих за точное измерение и дозировку различных ингредиентов, используемых для производства асфальтобетонной смеси. Этот блок играет критическую роль в обеспечении стабильного качества продукции, так как от точности дозировки зависит состав и характеристики готового материала.
Блок дозаторов состоит из нескольких отдельных дозирующих устройств, каждое из которых предназначено для определенного компонента: минеральных заполнителей (щебень, песок), битума, добавок и других возможных ингредиентов. Каждый дозатор представляет собой высокоточное устройство, оснащенное системами контроля веса и объема, что позволяет с большой точностью измерять необходимое количество каждого компонента.
Работа весов начинается с загрузки материалов в соответствующие бункеры. Эти бункеры снабжены датчиками уровня, которые контролируют количество материала внутри и сигнализируют о необходимости пополнения. После этого материалы поступают в дозирующие устройства, где происходит их точное взвешивание.
Процесс дозировки управляется автоматизированной системой, которая контролирует все параметры и следит за точностью измерений. Оператор задает нужные пропорции компонентов через панель управления в кабине оператора, после чего система автоматически распределяет материалы в соответствии с заданными параметрами. Это позволяет минимизировать человеческий фактор и значительно повысить точность и консистентность дозировки.
Важным аспектом работы весов является их способность к быстрому и точному изменению дозировок в зависимости от требований текущего производственного задания. Это особенно актуально для мобильных асфальтосмесительных установок, работающих с различными рецептами асфальтобетонной смеси, которые могут изменяться в зависимости от типа дорожного покрытия, климатических условий и других факторов.
Техническое обслуживание блока дозаторов включает регулярную калибровку весовых датчиков, проверку работы автоматизированной системы и очистку дозирующих устройств. Это необходимо для поддержания высокой точности и надежности работы оборудования, а также для предотвращения возможных сбоев и остановок производства.
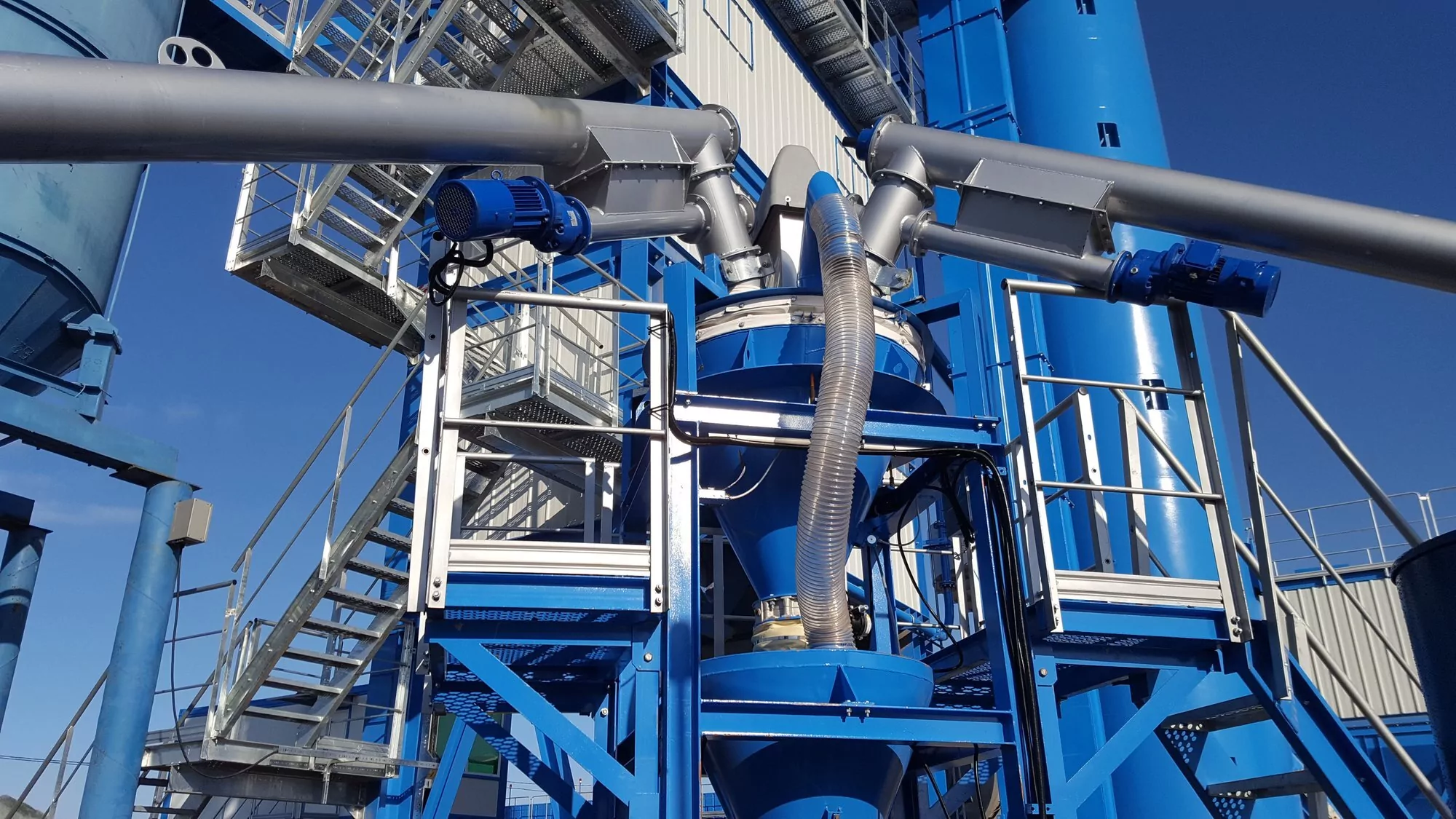
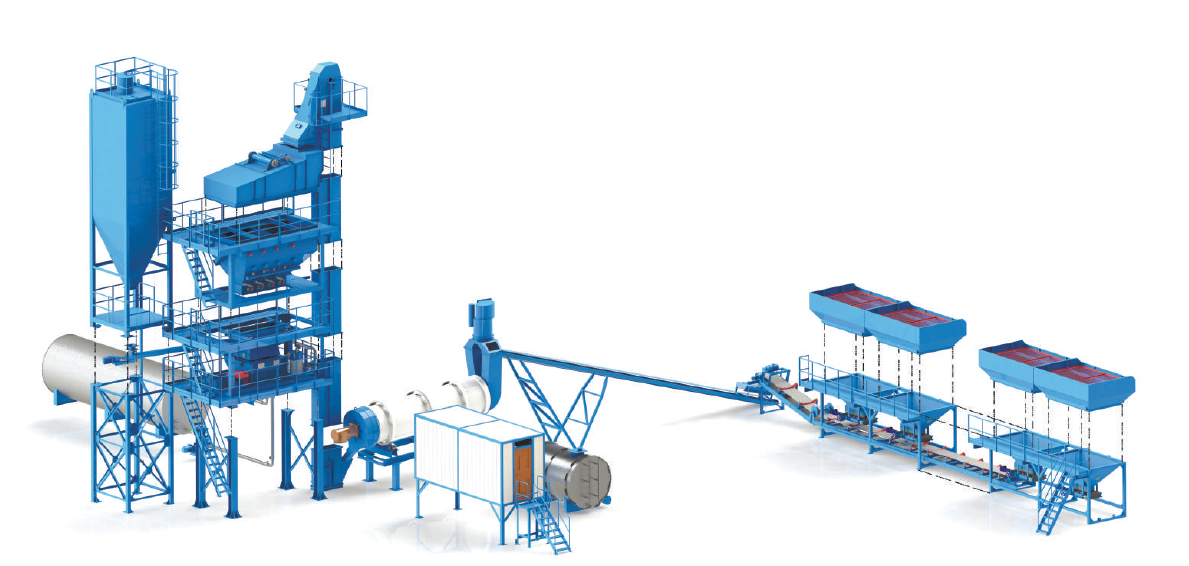
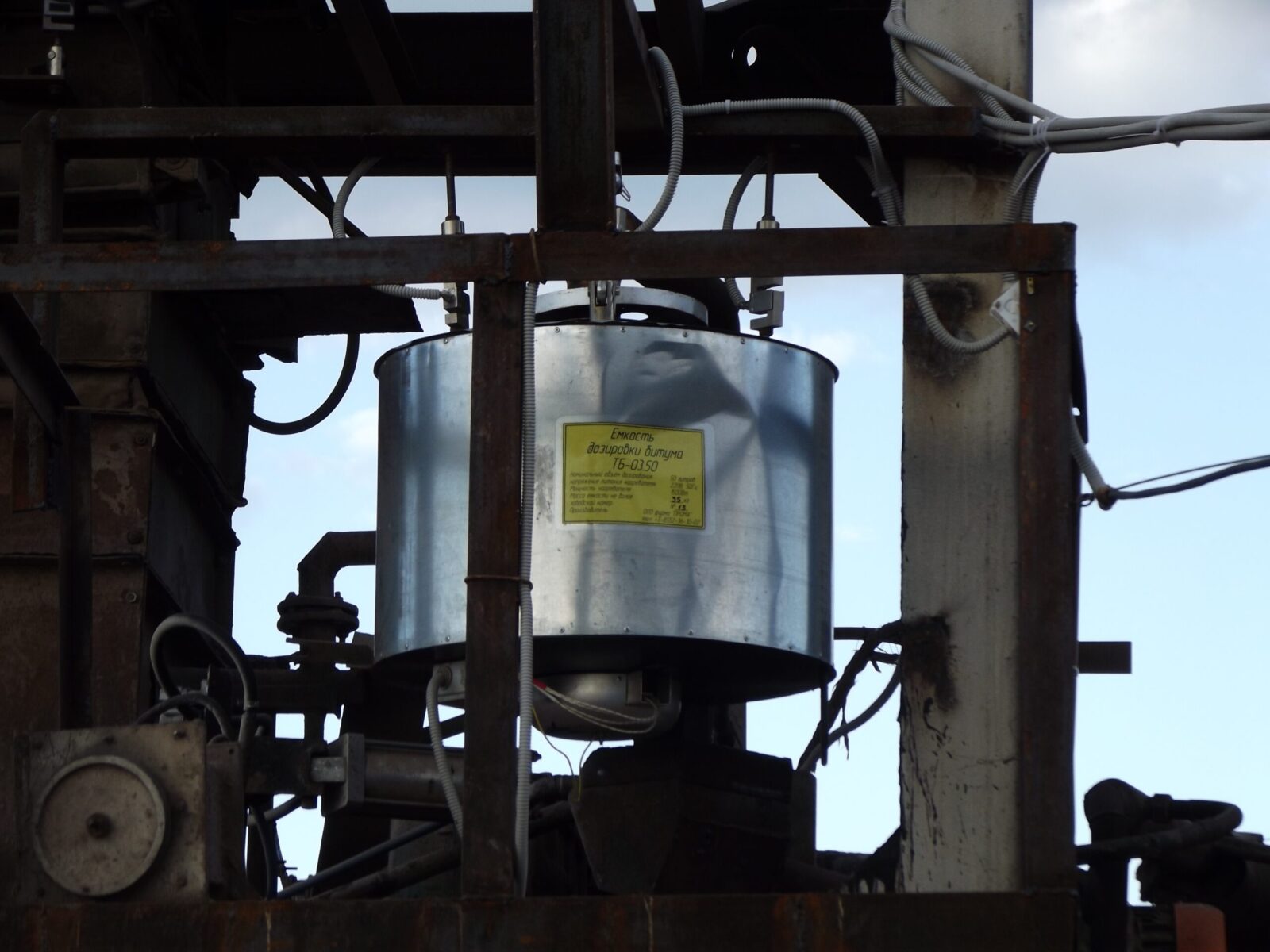
Смеситель
Смесители в асфальтобетонном заводе (купить можно перейдя на официальный сайт компании Мерко Руссланд) играют ключевую роль в процессе производства асфальтобетонной смеси, обеспечивая ее равномерное смешивание и гомогенизацию компонентов. Правильная эксплуатация смесителя играет важную роль в обеспечении успешной работы всего завода.
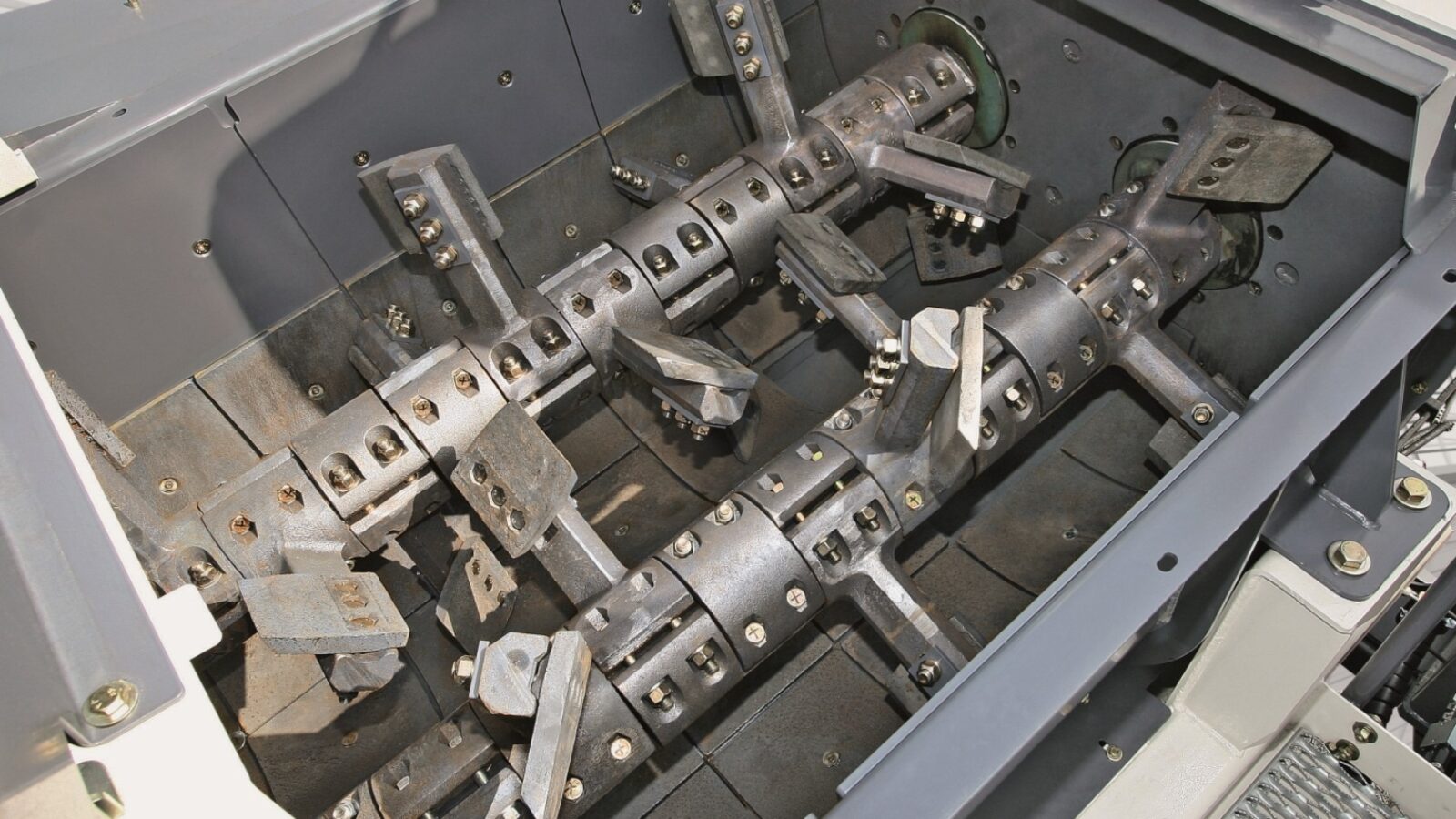
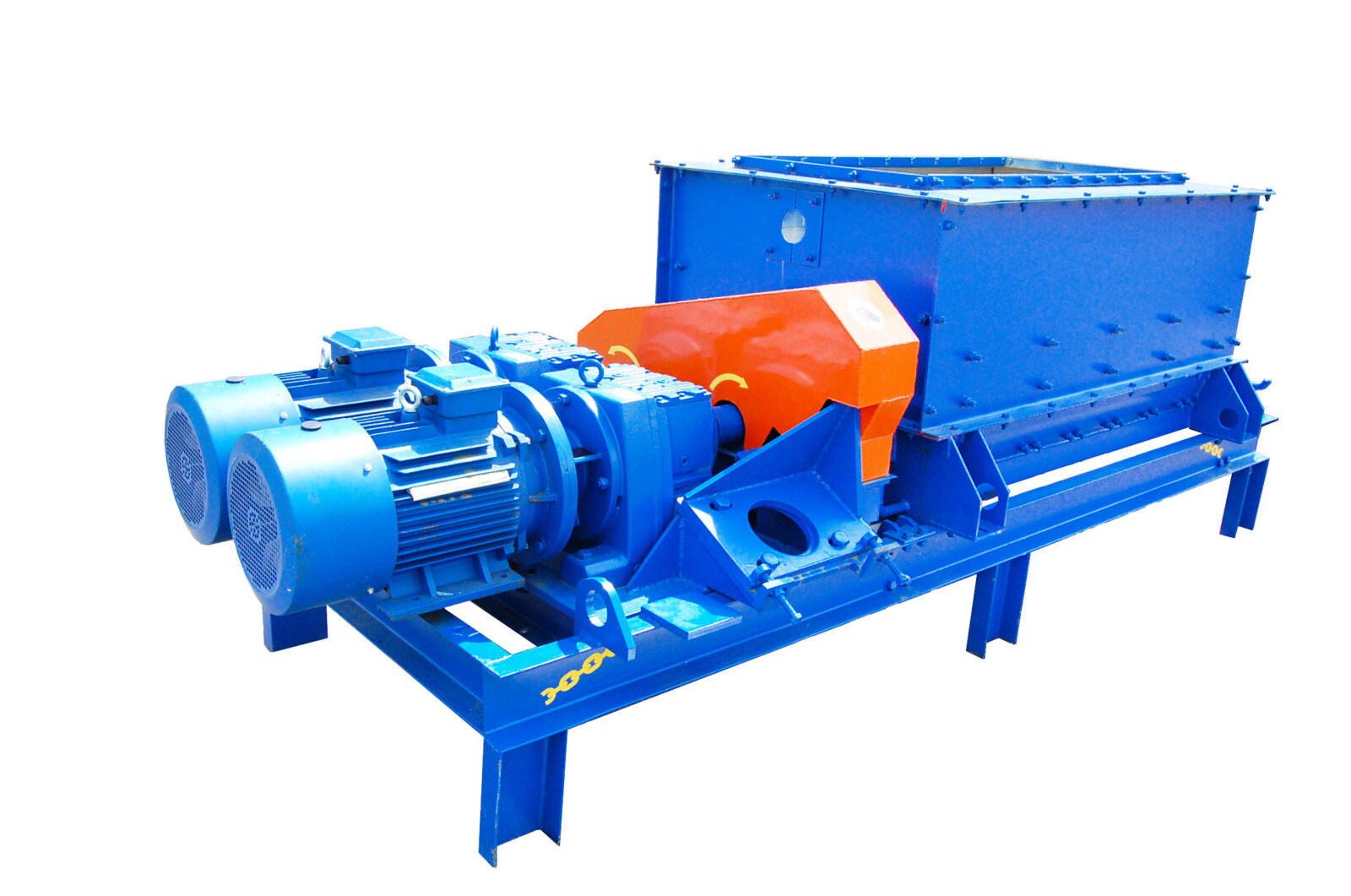
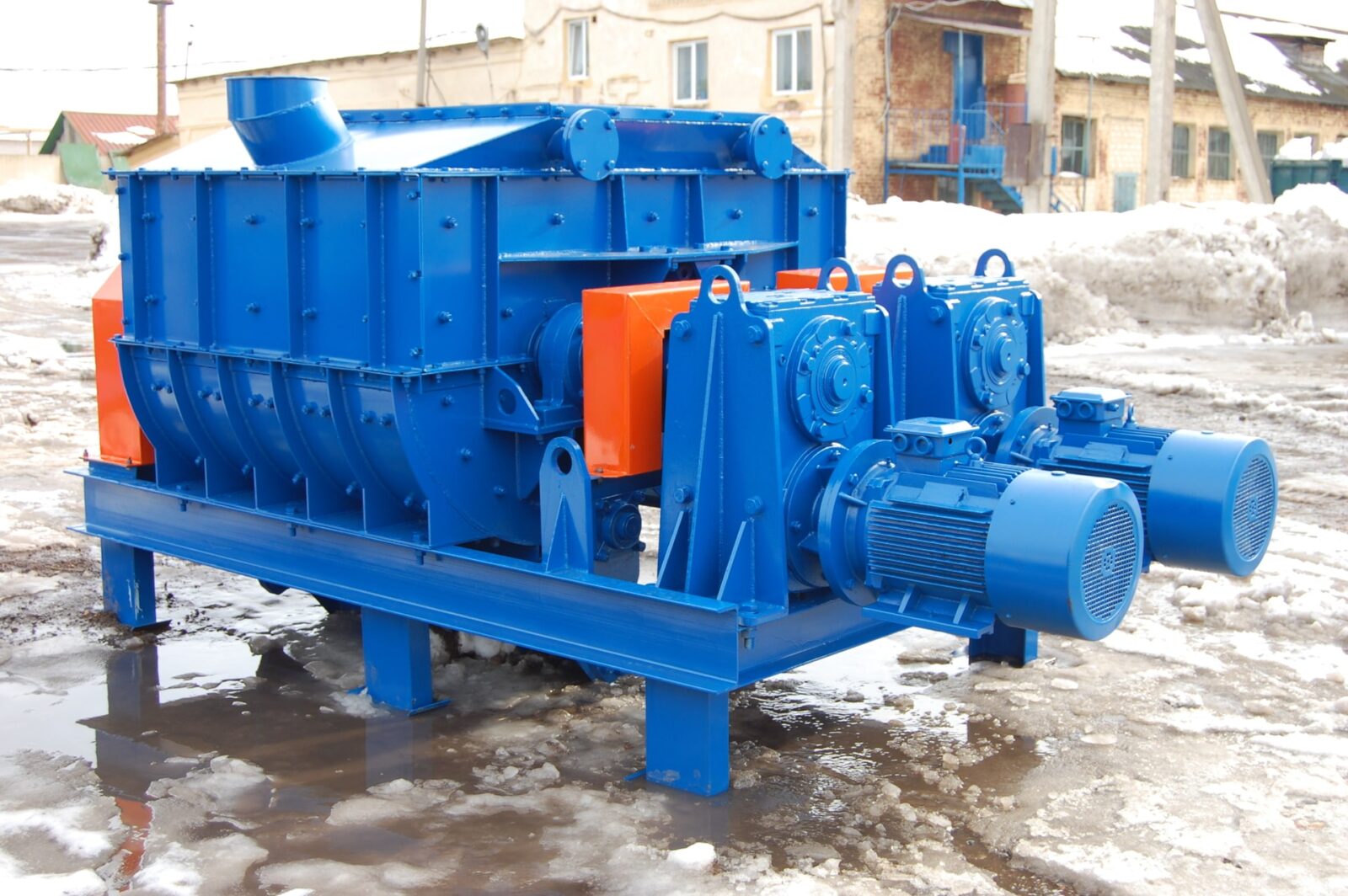
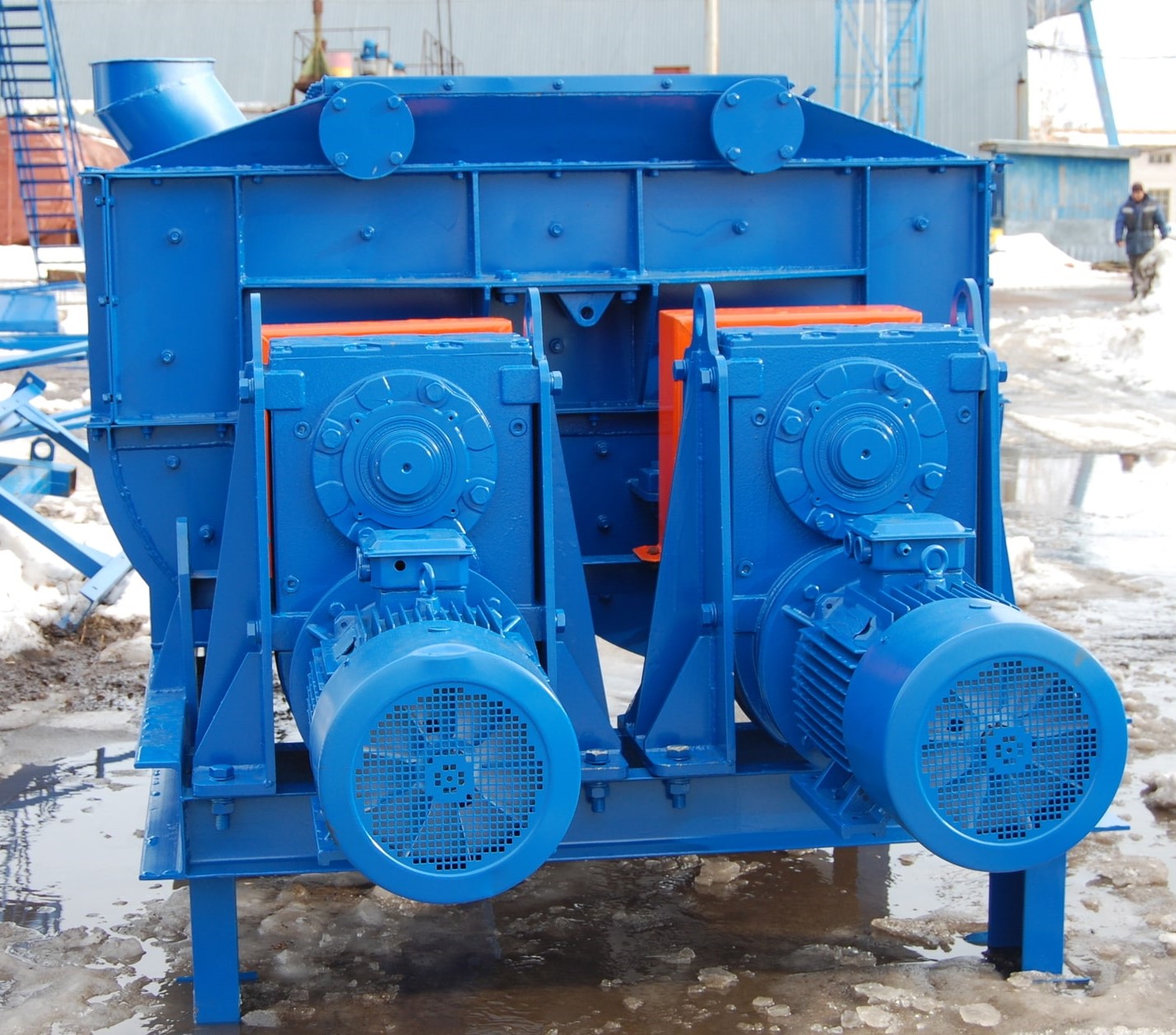
Агрегат минерального порошка и пыли
Агрегат минерального порошка и пыли играет ключевую роль в процессе производства асфальтобетонной смеси. Этот агрегат отвечает за подготовку, хранение и подачу минерального порошка, а также за управление и утилизацию пыли, образующейся в ходе различных производственных процессов.
Минеральный порошок является важным наполнителем в составе асфальтобетонной смеси. Он способствует улучшению физических и механических свойств готового материала, повышая его прочность, устойчивость к воздействию воды и долговечность. Основными источниками минерального порошка могут быть дробленый известняк, доломит, мрамор или другие минеральные материалы, которые предварительно измельчаются до состояния мелкой пыли.
Агрегат минерального порошка и пыли состоит из нескольких основных элементов.
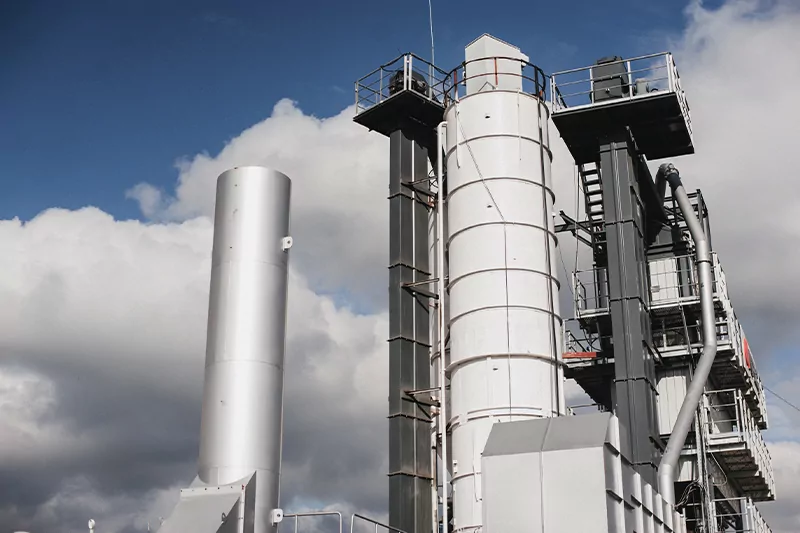
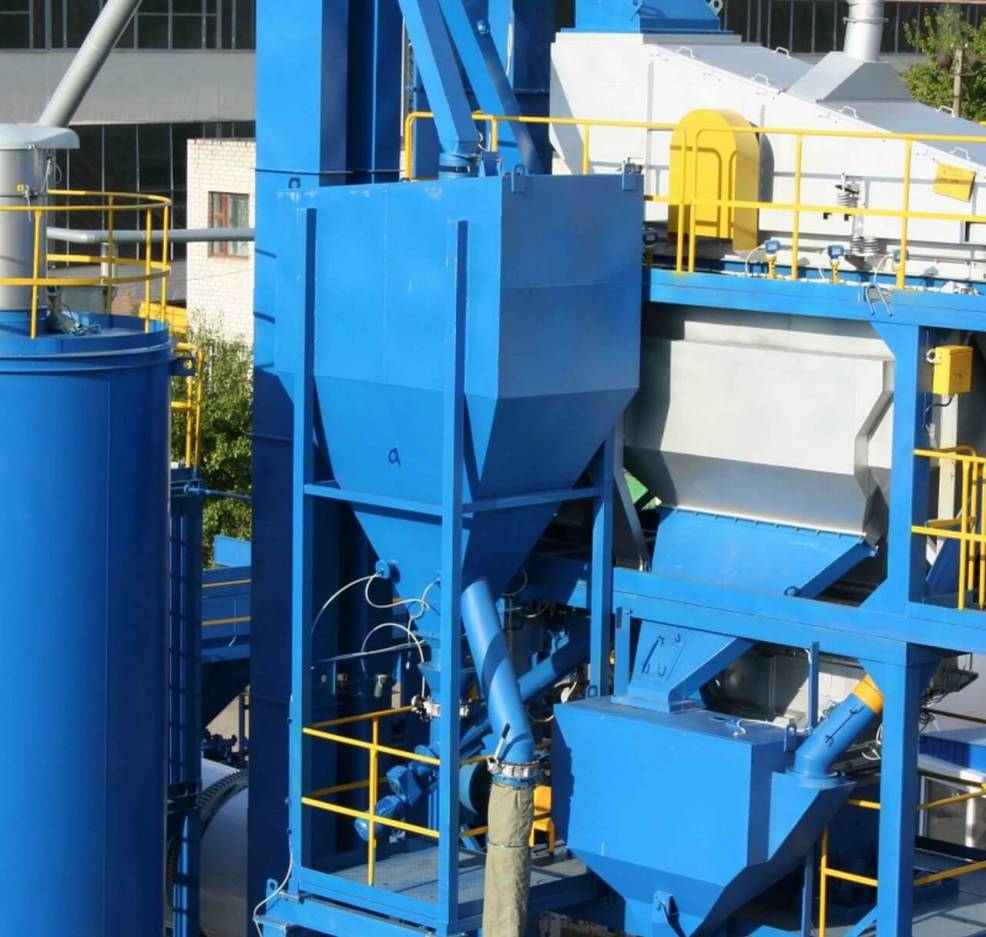
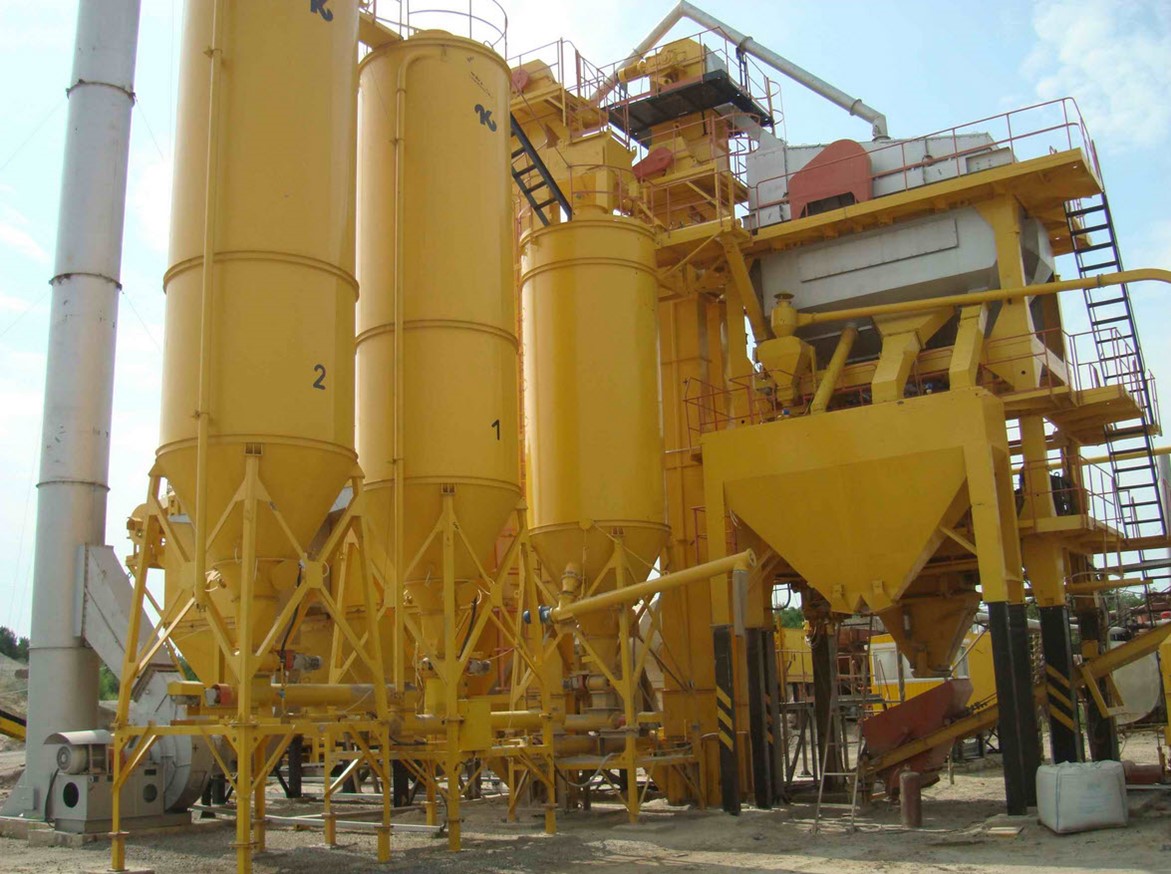
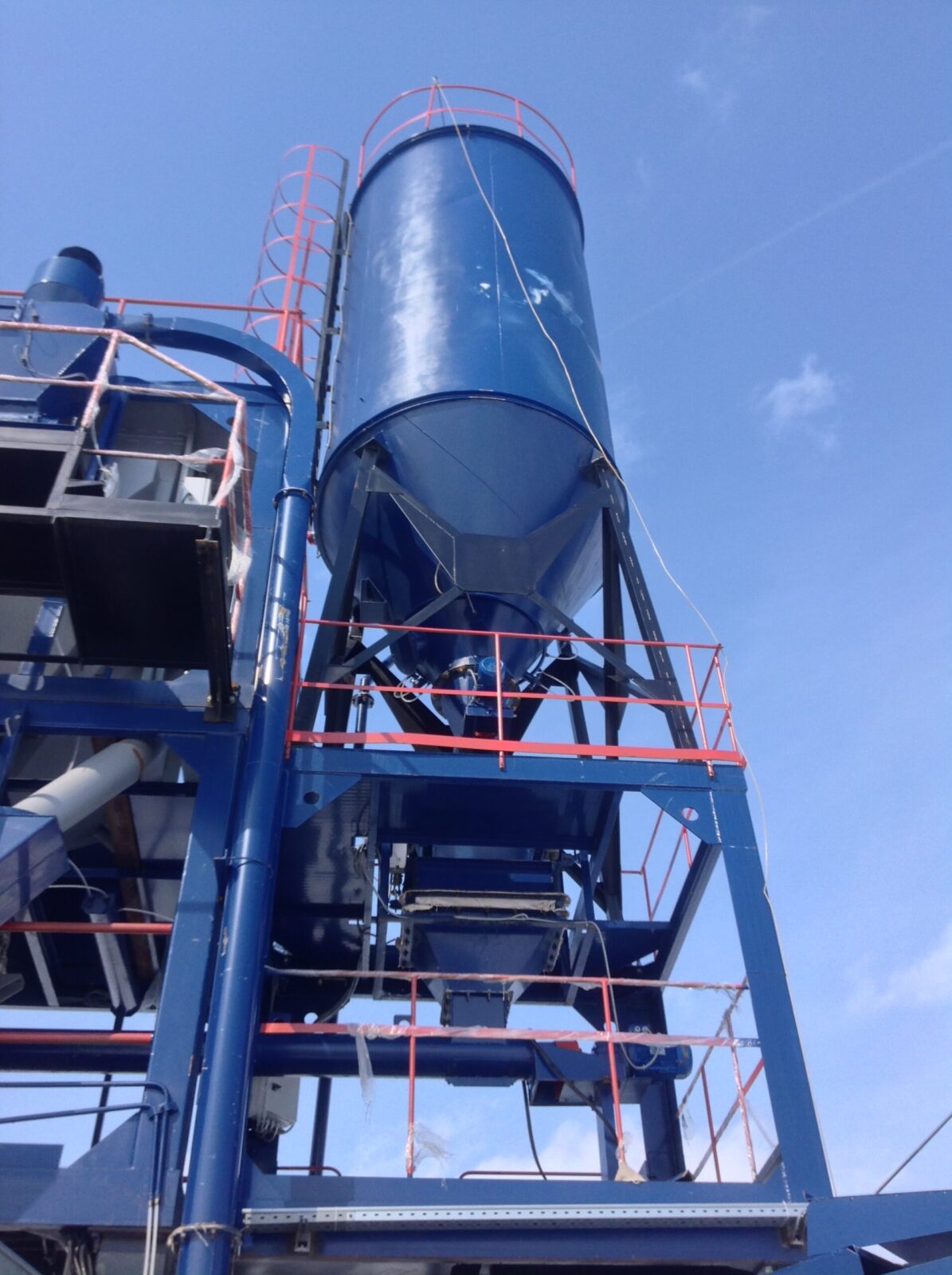
Пневмосистема АБЗ
Пневмосистема асфальтобетонного завода – это сложная и многофункциональная система, предназначенная для обеспечения работы узлов и агрегатов АБЗ (заслонки, продувка фильтров и т.д.) Она играет ключевую роль в обеспечении эффективной работы АБЗ, автоматизации производственных процессов и поддержании высокого качества конечного продукта.
Основные компоненты пневмосистемы асфальтобетонного завода включают.
- Компрессоры. Эти устройства служат для сжатия воздуха, который затем используется для транспортировки материалов. Компрессоры должны обеспечивать стабильное давление воздуха и достаточную производительность для нужд завода.
- Пневматические транспортные линии. Состоят из трубопроводов, по которым сыпучие материалы перемещаются с помощью сжатого воздуха. Транспортные линии могут быть как горизонтальными, так и вертикальными, что позволяет эффективно доставлять материалы в нужные участки завода.
- Пневматические клапаны и заслонки. Эти устройства регулируют поток материалов и воздуха в системе. Они обеспечивают точное распределение компонентов и предотвращают возможные потери или засоры в транспортных линиях.
- Фильтры и сепараторы. В процессе транспортировки пневмосистема может захватывать мелкие частицы и пыль. Фильтры и сепараторы предназначены для очистки воздуха от этих примесей, обеспечивая чистоту и надежность работы системы.
- Контрольные и измерительные приборы. Включают датчики давления, расходомеры, уровнемеры и другие устройства, которые следят за параметрами работы пневмосистемы. Они позволяют операторам завода контролировать процесс и своевременно реагировать на отклонения или сбои.
- Пневмоцилиндры и актуаторы. Используются для автоматизации различных механизмов и процессов на заводе. Например, они могут управлять открытием и закрытием заслонок, регулировать подачу материалов и выполнять другие задачи.
Пневмосистема обеспечивает ряд важных преимуществ для работы асфальтобетонного завода.
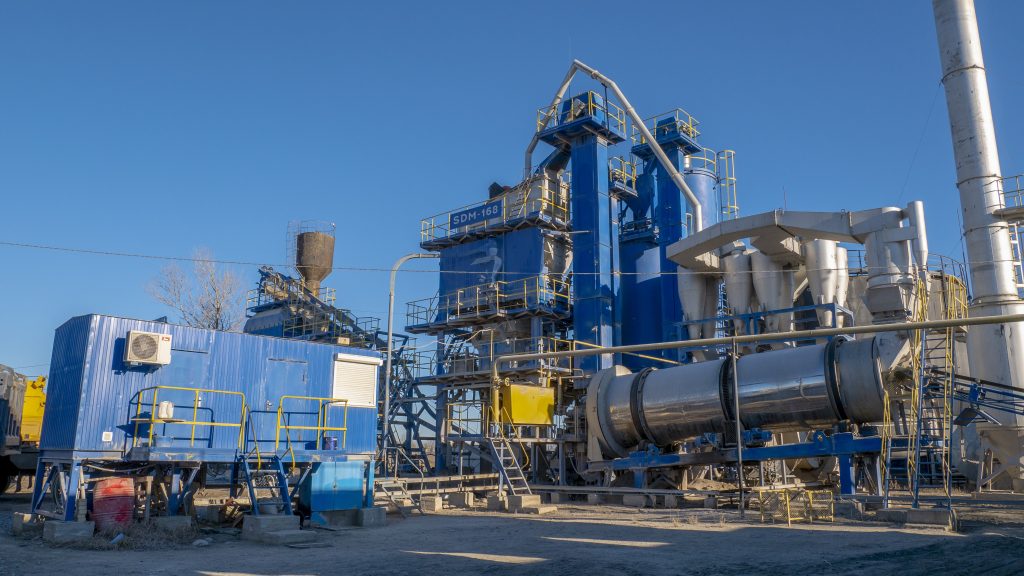
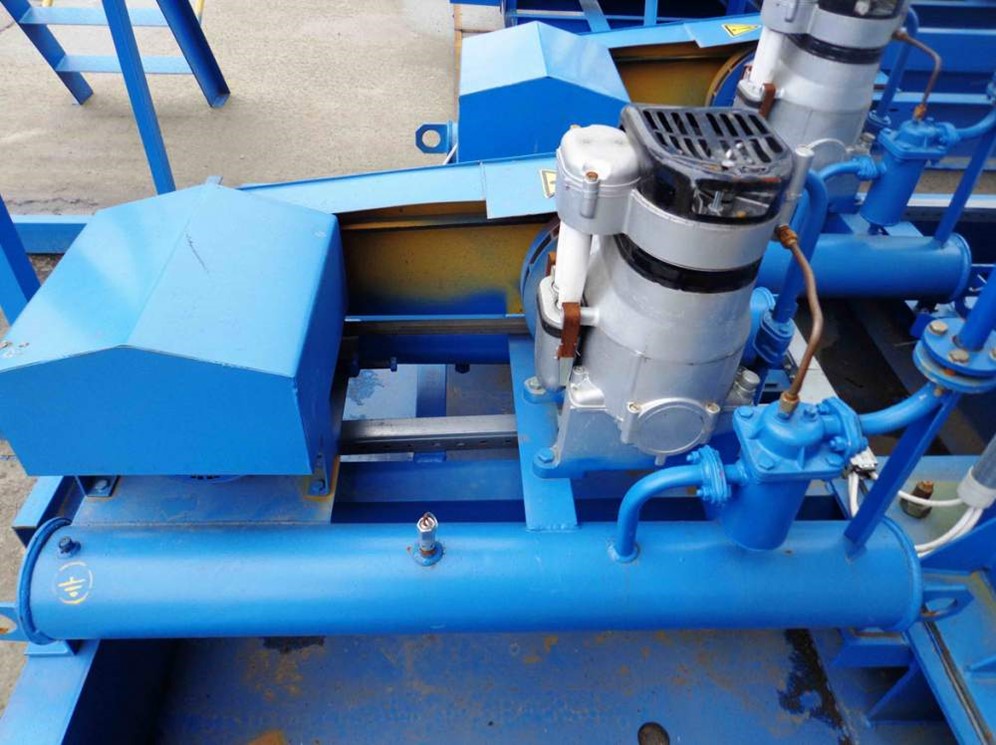
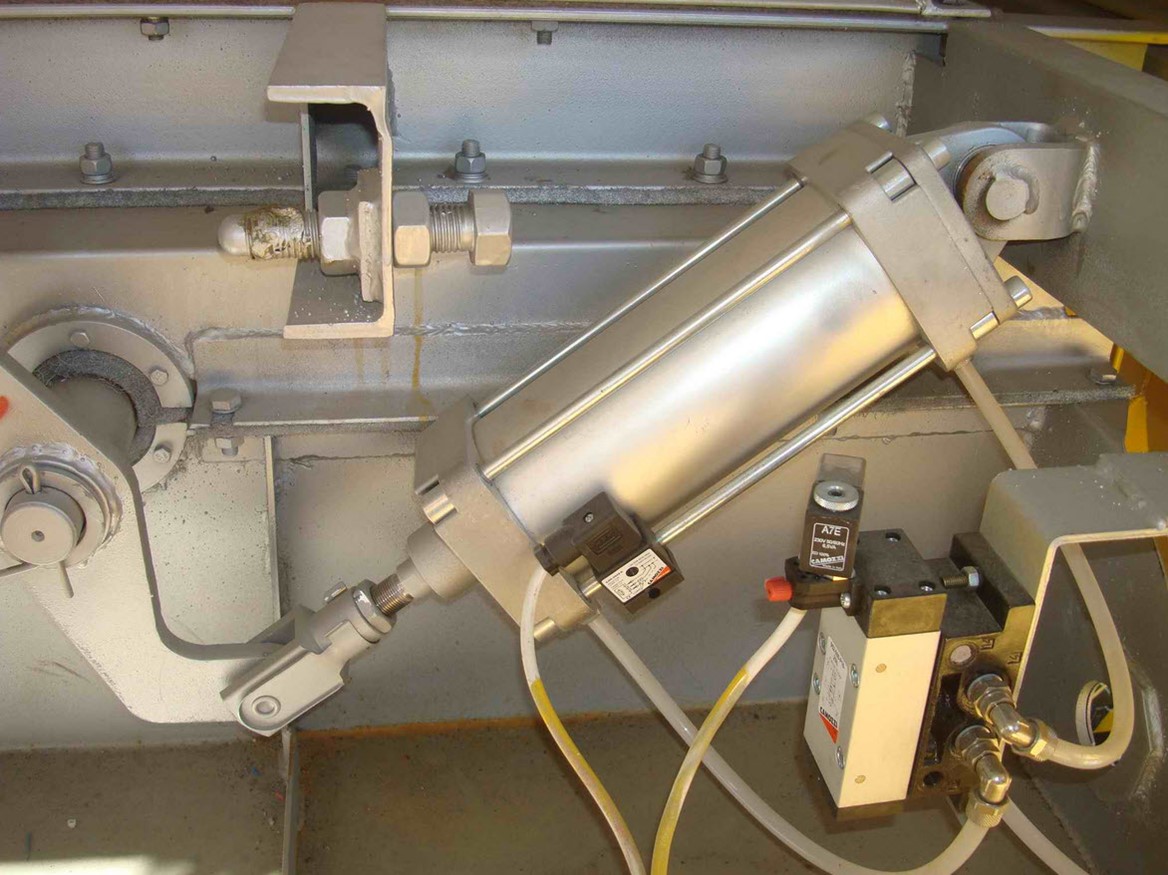
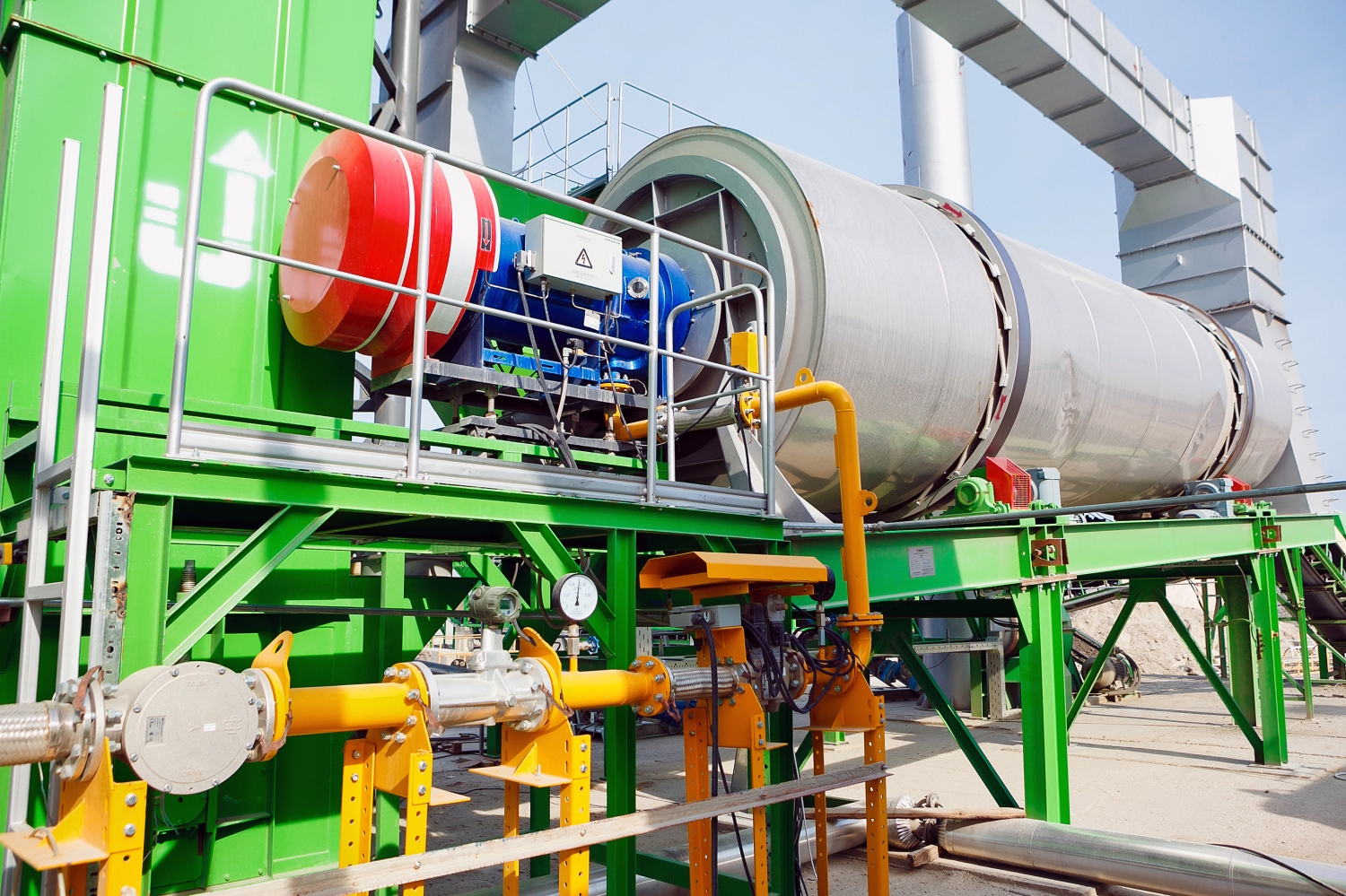
Кабина оператора
Кабина оператора асфальтобетонной установки – это специализированное помещение, откуда осуществляется управление всем производственным процессом. Этот элемент предприятия играет ключевую роль в обеспечении бесперебойной работы оборудования и контроля качества продукции.
Кабина оператора обычно располагается в непосредственной близости к основным производственным линиям, что позволяет оператору иметь хороший обзор всего производственного процесса. Современные кабины оснащены панорамными окнами и системами видеонаблюдения, что обеспечивает полный контроль над происходящим на АСУ.
Внутри кабины находятся различные панели управления, компьютеры и мониторы, с помощью которых оператор контролирует и управляет всеми аспектами производства асфальтобетонной смеси. Панели управления включают в себя множество кнопок, переключателей и индикаторов, которые позволяют оператору запускать и останавливать оборудование, регулировать температуру, давление и другие параметры, необходимые для производства качественной продукции.
Компьютерные системы, используемые в кабине оператора, обеспечивают автоматизацию многих процессов. Они позволяют оператору следить за текущими параметрами производства в реальном времени, а также получать предупреждения о возможных неисправностях или отклонениях от заданных параметров. Это значительно упрощает процесс управления и повышает его эффективность.
Кроме того, кабина оператора оснащена системами связи, что позволяет оперативно передавать информацию и получать указания от руководства завода или других специалистов. Это важный аспект, особенно в случаях возникновения непредвиденных ситуаций, требующих быстрого реагирования.
Важным элементом кабины оператора является система кондиционирования и отопления, которая обеспечивает комфортные условия работы для оператора независимо от внешних погодных условий. Также кабина может быть оборудована средствами для обеспечения безопасности, такими как огнетушители, аварийные выходы и системы оповещения.
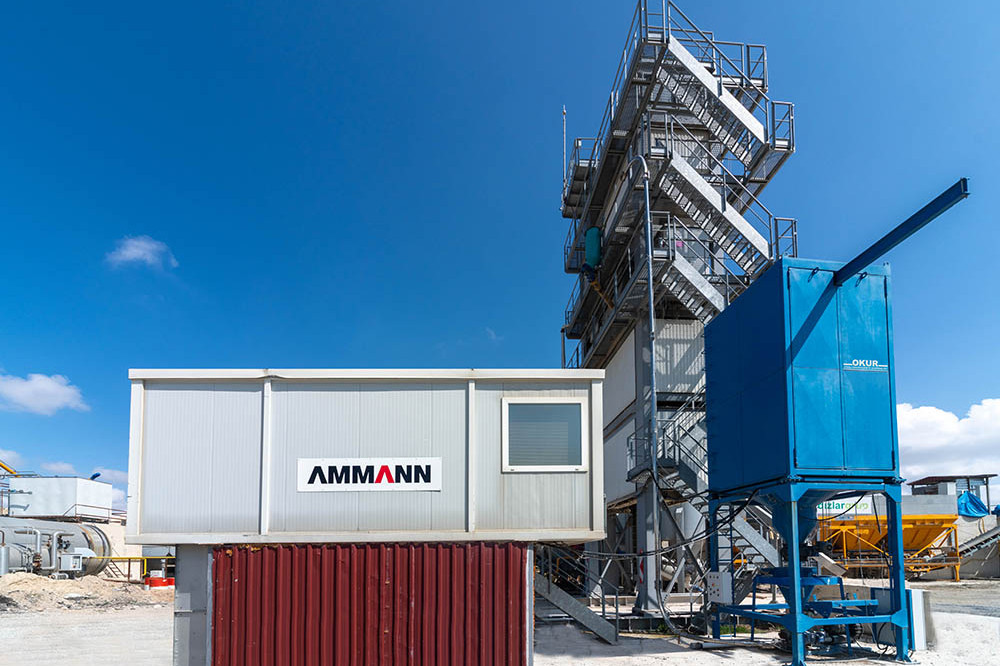
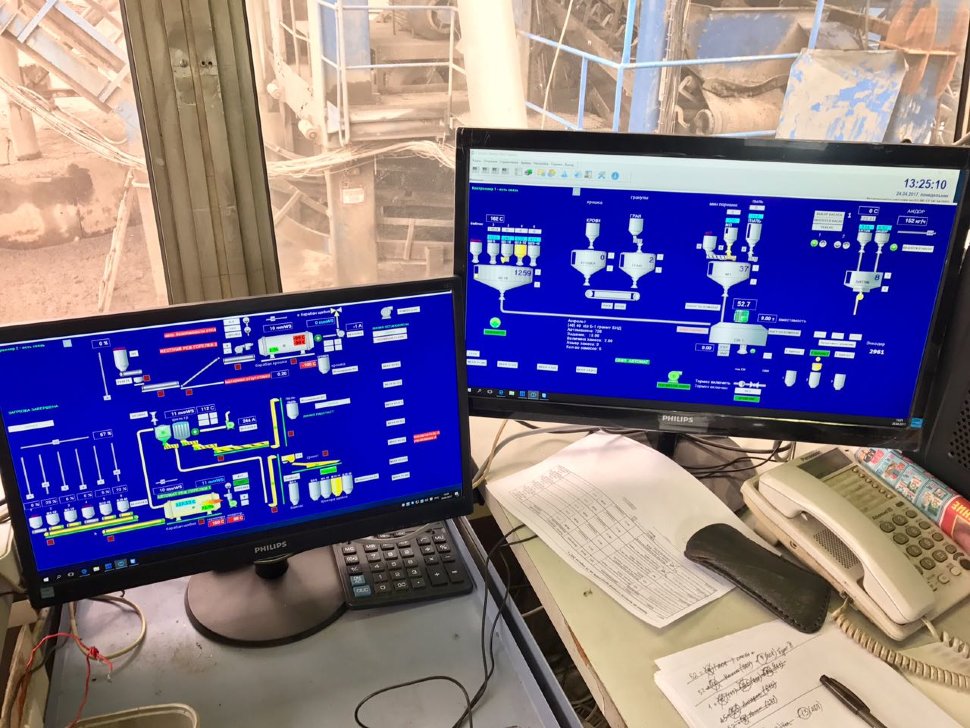
